Product lines
The coolness factor of an aluminium bottle can be hardly overestimated. This lightweight, unbreakable and recyclable bottle has found its way into the market. Fancy printing and unique shaping guarantee the desired brand recognition. Producers world-wide are convinced by our machinery and its core competences: Forming of a hollow body either by Impact Extrusion or DWI, trimming, printing, necking and shaping.
IE Production Lines
Production lines using an impact extrusion press to form a hollow cylinder out of an aluminium slug by one stroke. The cylinder is subsequently cut to length, decorated, necked and shaped to an Aluminium Bottle.
CMC 200
This line is the workhorse of the industry. It is used everywhere on the planet for the production of monoblock aluminium containers with a production speed up to 200 cpm. Being available in three different diameter ranges: 20-45 mm, 35-53(59) mm and 45-66 mm, the line can be used to offer a great variety of solutions to your customers in the beverage markets.
Packing machine
for strapping aluminium bottles in bundles or layer blocks for pallet packing
Special features
- Ideal for aluminium bottles
- Optimal grouping of bottles
- Fast and gentle strapping via servo-controlled process
- Synchronous bottle transport from the upstream machine
- High production reliability and security
- Supplement machine to palletize the bundles are available
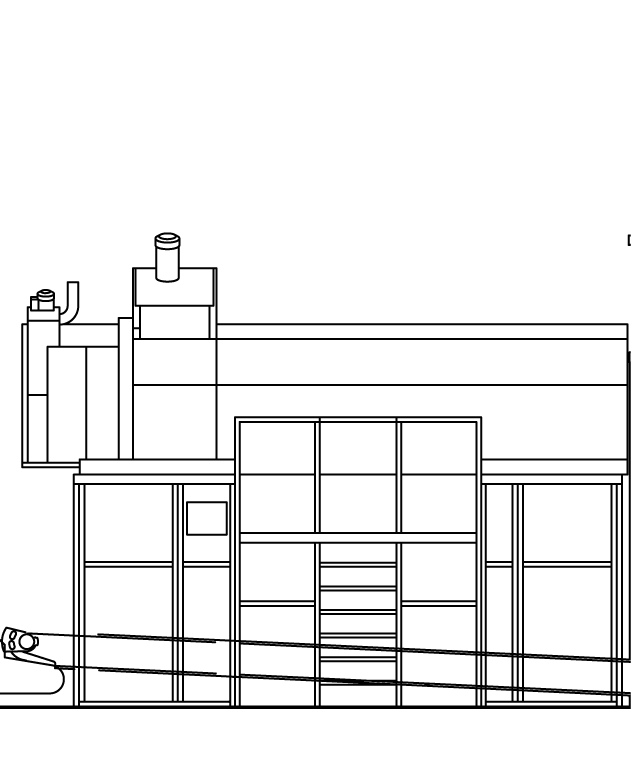
Postwasher
Our customized postwashing machines are equipped with a patented spraying system to ensure low water consumption.
A bypass function for the transport without washing/rinsing is included as standard.
Technical data
Type | PWM 45 | PWM 55 | PWM 66 | PWM 80 |
---|---|---|---|---|
Max. Diameter (mm) | 45 | 55 | 66 | 80 |
Chain pitch | 3 x ¾” | 4 x ¾” | 5 x ¾” | 6 x ¾” |
Number of washing / rinsing cabins | 2 | 2 | 2 | 2 |
Special features
- Stainless steel design, cabins equipped with windows
- Washing of the bottles in the first washing/rinsing cabin
- Rinsing of the bottles in the following rinsing cabins
- All cabins equipped with a patented spraying system with low water consumption
- Electrically heated tank for the first washing/rinsing cabin equipped with pumps, level control and temperature regulation
- Dripping area after washing, vertically arranged pins and drying blades
- Automatic level control of the tanks, equipped with safety unit against water shortage, temperature monitoring unit
- Stainless steel tank for collecting the dripping water below the washing machine
- Drying of the bottles in the gas heated oven, low-energy design
- Chain guides made of PTFE (Teflon)
- Additional blowing nozzles for drying the interior and the rim of the bottles
- Reliable system for sucking off the oven exhaust air
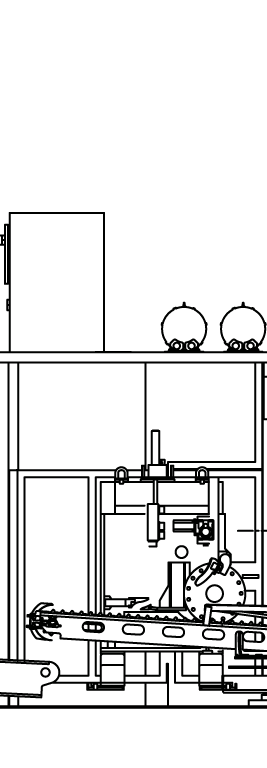
Leak detector
A photocell is used to detect if rays of light fall into the bottle through micro-holes. Defective bottles are automatically ejected at the outfeed conveyor after the Leak detector. A 100% quality-control ensures that only complete secure bottles leave the line.
The Leak detector can be placed on the outfeed conveyor of the Necking machine. Alternatively it can be integrated as a stand-alone machine in the line.
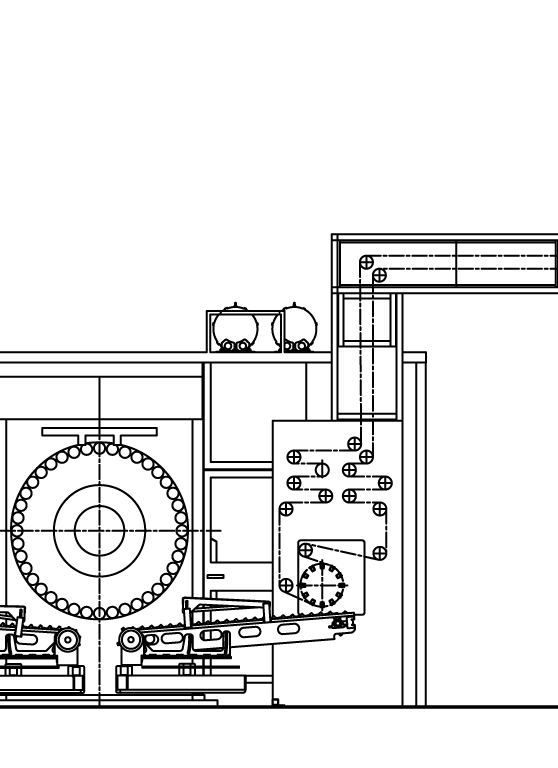
Necking machine
The cylinder is necked and shaped by necking dies up to the final bottle design. Processes as threading, curling, beading, registered embossing and debossing to create unique shapes and designs fitting the needs of your customers.
Any combination to create a 56 or 80 or 84 station necker system for advanced/modified alloys or DWI are possible.
Technical data
Type | C200.28 | C200.28.VE | C200.36XVE | C200.40VE |
---|---|---|---|---|
Can diameter (mm) | 35-66 | 35-66 | 35-80 | 35-66 |
Finished product length (mm after necking) | 110 – 250 | 110 – 250 | 110-275 | 105 – 250 |
Number of stations | 28 | 28 | 36 | 40 |
Total stroke (mm) | 150 | 132/216/280 | 110 - 270 | 110 - 270 |
Usable stroke (mm) | 90 | 90/143/180 | 80 - 187 | 80 - 187 |
Special features
- Pneumatic holding grippers with electronic control for bottle detection guarantee a constant stable position of the bottle
- Tool quick-change system for maximum product flexibility
- Compressed air-assisted necking to enable even complicated shapes
- Bottom forming unit included in the standard supply
- Maximum accessibility to the machine working area for easy handling and setting of the tools
- Optimized bottle transfer systems between conveyors and drums
- Infinitely adjustable stroke (C200.36XVE and C200./C250.40VE)
- Electronic presetting device to set lubrication cycle frequency
- Possible application of all our proprietary tools allowing wide machining possibilities
- Frequency-controlled motors for rotating tools (C200.36XVE and C200./C250.40VE)
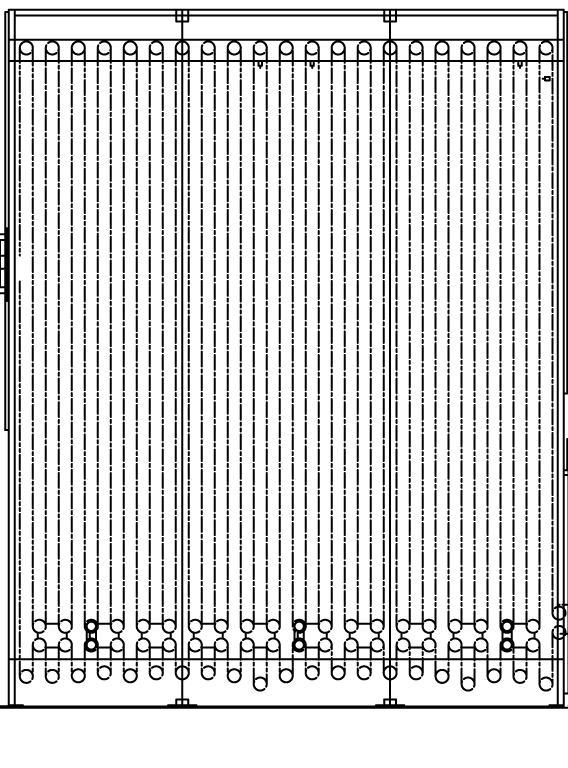
Accumulator 3
for accumulating the cylinders and compensating the asynchronous operation of decoration unit and necking machine.
Special features
- Two-part welded frame, mounted onto the floor with a capacity of 2000 cans
- Constant chain tension system
- Safety covering of the accumulator up to a height of 2,5 m with acrylic glass panes at the front side, rear and top with sheet metal covering. A complete covering of the accumulator is optionally available
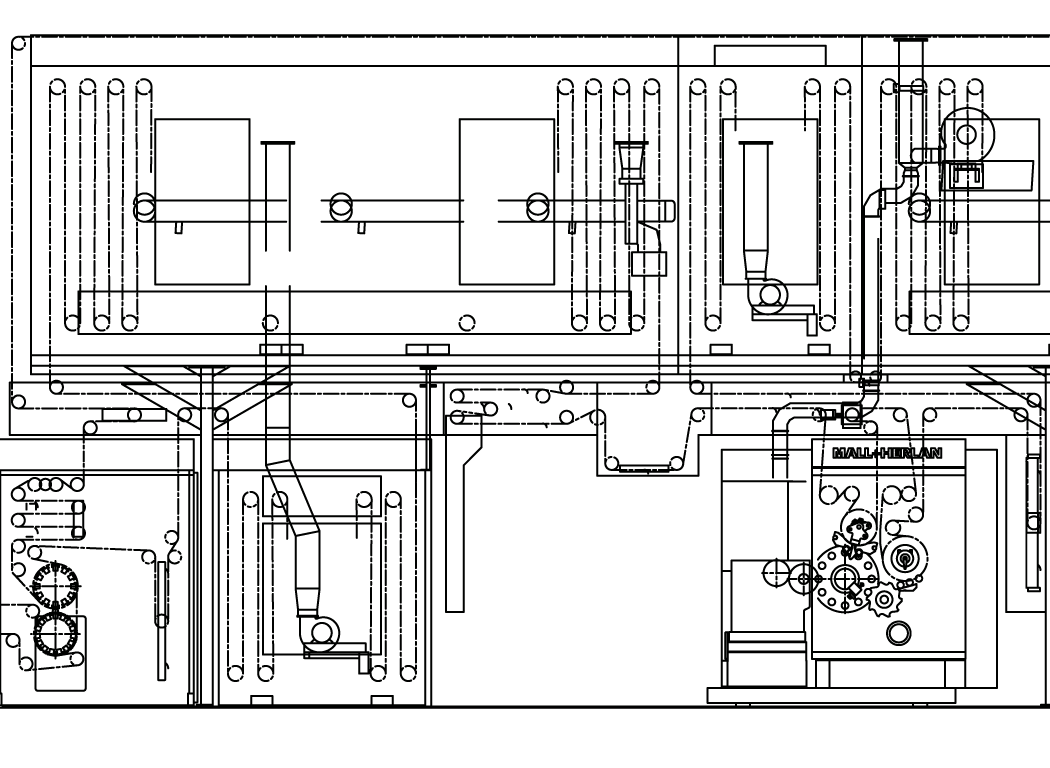
Overvarnish lacquering machine
The overvarnish is applied to protect the decoration. According to the request of your customers also special effects like matt, semi matt, gloss or haptic can be provided.
Special features
- Cylinder transfer from the conveyor chain to a mechanical take-off drum with size-independent vacuum pockets
- Mechanical indexing gear unit with 12 stations
- Mandrel quick change unit and monitoring of the correct clamping
- Infinitely variable mandrel drive by means of controlled servomotor
- Vacuum-assisted loading and steadying of the cylinders on the mandrels, before and during processing
- Three roller base-coating unit designed as V-type-coating unit
- Transfer unit with take-off control and two suction units for transporting the cylinders from the mandrels onto the chain pins
- Oven chamber with integrated chain guide
- Sprocket bearings with re-lubricating facility, installed outside the oven in an aluminium casing sealed towards the rear wall of the oven
- Possibility of cylinder sampling for test purposes from the pins of the dryer chain, after drying of the clear varnish.
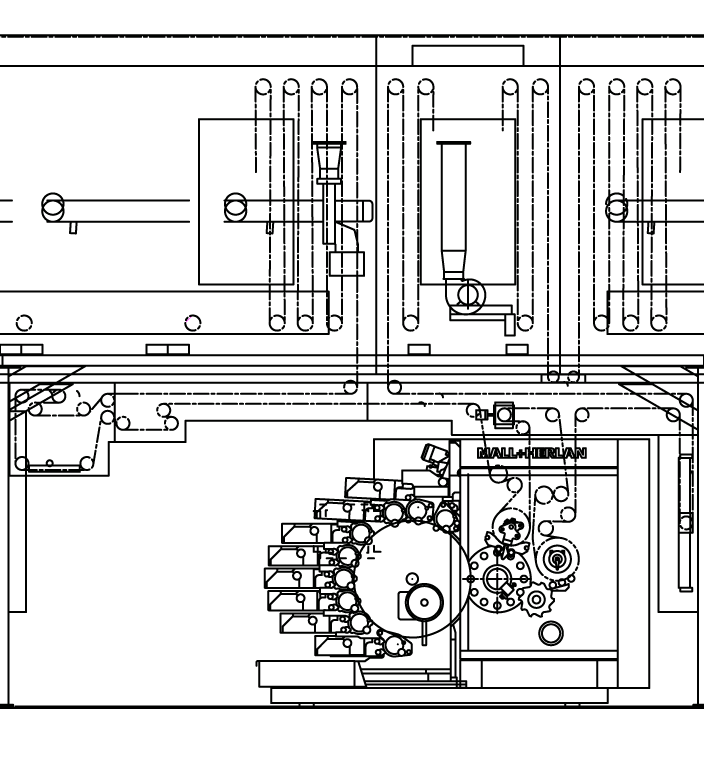
Printing machine
The printing unit, which can apply up to 9 colours, ensures the widest possible decoration variety for aluminium bottles
Special features
- Cylinder transfer from the conveyor chain to a mechanical take-off drum with size-independent vacuum pockets
- Mechanical indexing gear unit with 12 stations
- Mandrel quick change unit and monitoring of the correct clamping
- Infinitely variable mandrel drive by means of controlled servomotor
- Vacuum-assisted loading and steadying of the cylinders on the mandrels, before and during processing
- Printing unit with up to 9 colours
- Transfer unit with take-off control and two suction units for transporting the cylinders from the mandrels onto the chain pins
- Oven chamber with integrated chain guide
- Sprocket bearings with re-lubricating facility, installed outside the oven in an aluminium casing sealed towards the rear wall of the oven
- Possibility of cylinder sampling for test purposes from the pins of the dryer chain, after drying of the printing inks.
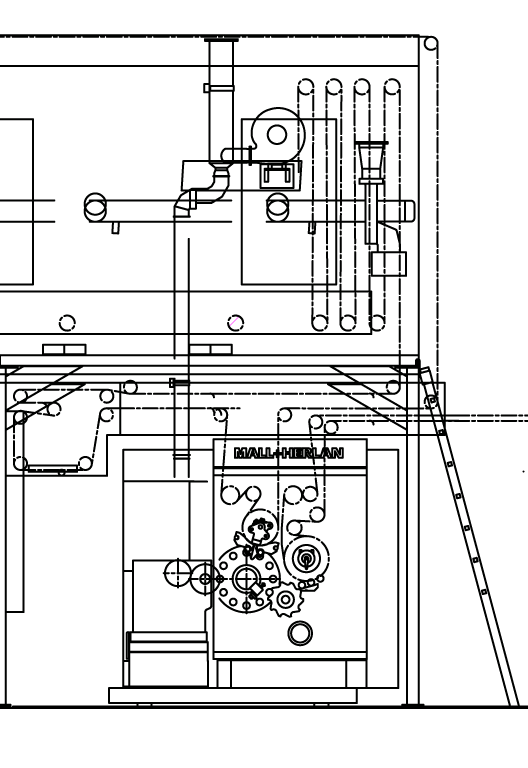
Basecoat lacquering machine
The cylinder receives the base coat which is important for the stain resistance and excellent print quality. The base coat is dried in the first oven chamber of the decoration drying oven.
Special features
- Cylinder transfer from the conveyor chain to a mechanical take-off drum with size-independent vacuum pockets
- Mechanical indexing gear unit with 12 stations
- Mandrel quick change unit and monitoring of the correct clamping
- Infinitely variable mandrel drive by means of controlled servomotor
- Vacuum-assisted loading and steadying of the cylinders on the mandrels, before and during processing
- Three roller base-coating unit designed as V-type-coating unit
- Transfer unit with take-off control and two suction units for transporting the cylinders from the mandrels onto the chain pins
- Oven chamber with integrated chain guide
- Sprocket bearings with re-lubricating facility, installed outside the oven in an aluminium casing sealed towards the rear wall of the oven
- Possibility of cylinder sampling for test purposes from the pins of the dryer chain, after drying of the basecoat
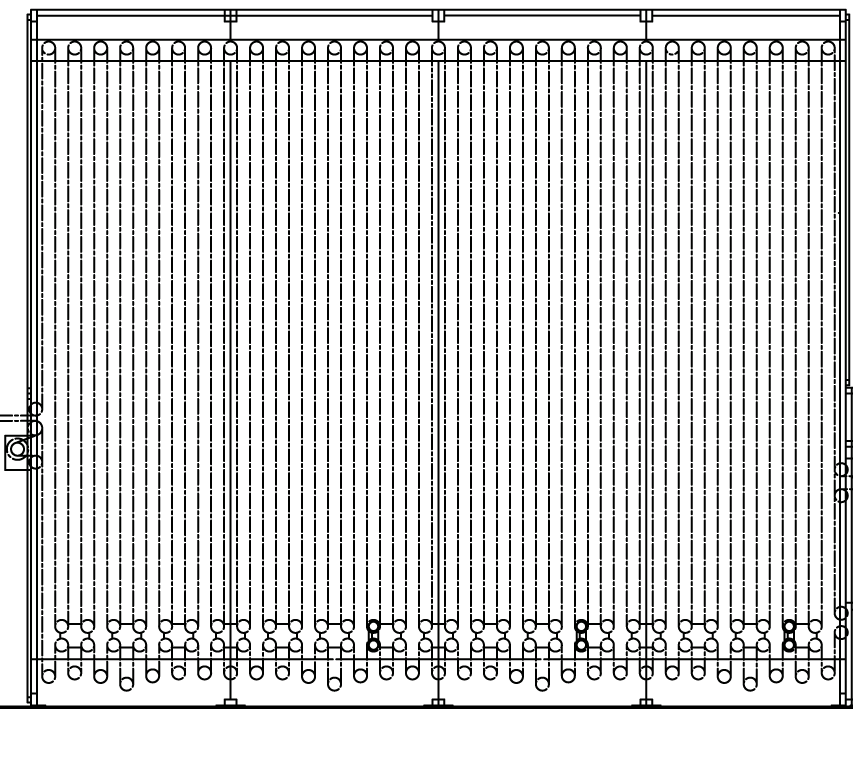
Accumulator 2
for accumulating the cylinders and compensating the asynchronous operation of internal coating machine and decoration unit.
Special features
- Four-part welded frame, mounted onto the floor with a capacity of 3250 cans
- Constant chain tension system
- Safety covering of the accumulator up to a height of 2,5 m with acrylic glass panes at the front side, rear and top with sheet metal covering. A complete covering of the accumulator is optionally available
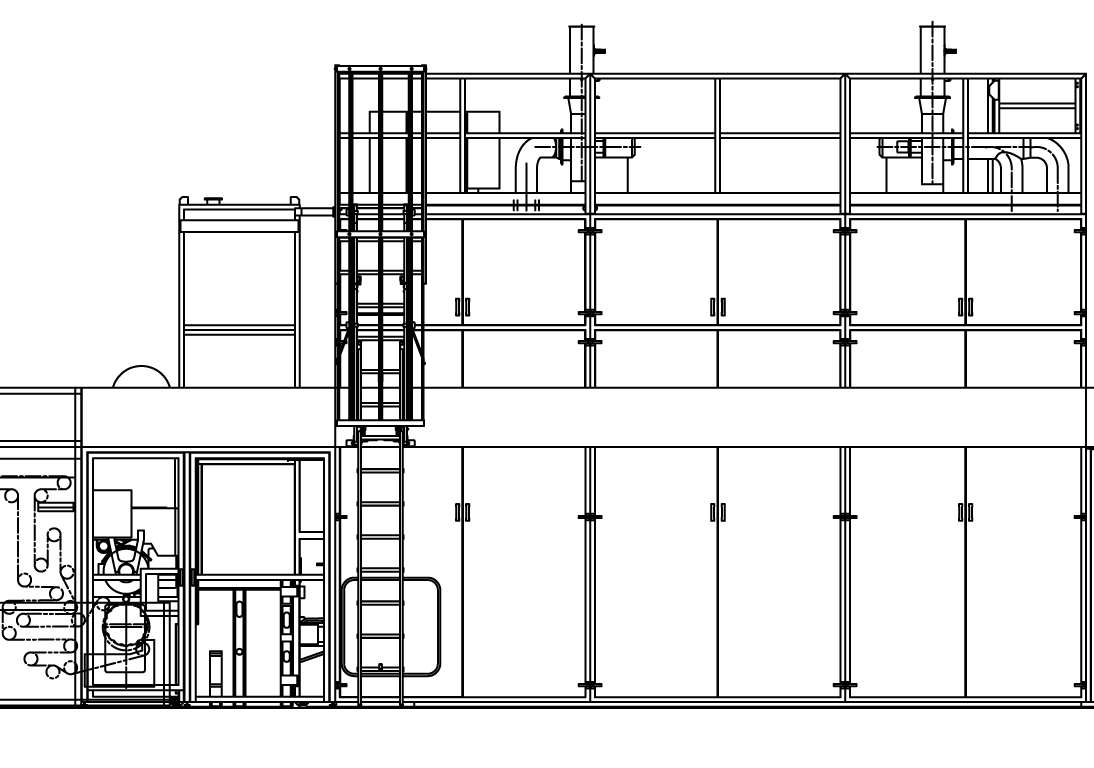
Internal coat dryer
for polymerizing the internal lacquer coat, electrically heated or alternatively by gas.
Special features
- 1,2 or 3 row transport chain with baskets
- Reduced wear-out of the transport chain and the chain wheels by cardan-based drive system
- Chain tension with weight, electronically monitored
- Easy accessibility to the dryer interior due to large doors
- Quadruple door look
- Isolated doors with special door hinges for synchronized door closing
- Large outer doors with smooth surface on the oven’s front and rear sides
- Quick and easy removal and reassembly of the shafts and chain wheels in case of service
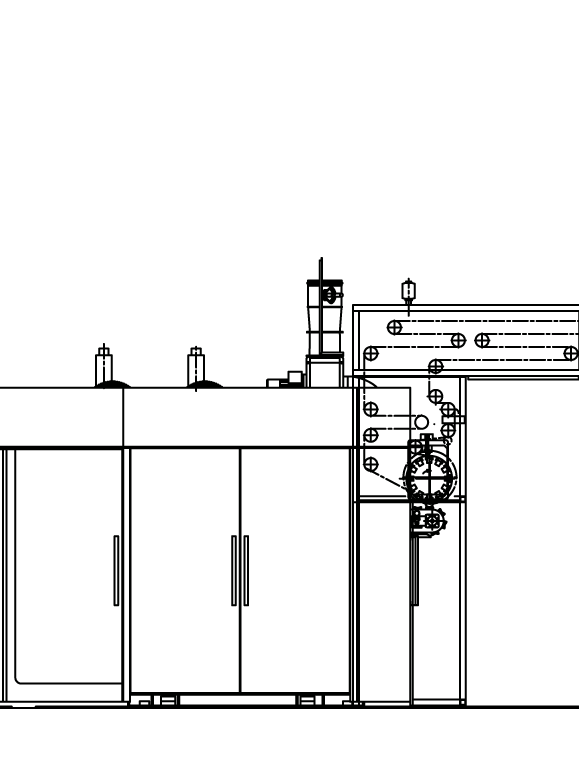
Internal coating machine
A functional lacquer is applied to seal the inside of the cylinder using moveable spray lances. In the following oven with its cooling zone the inside lacquer is cured and hardened.
Special features
- Low vibration due to solid mechanical design
- Individual vacuum circuit for machine infeed and outfeed
- Increased user comfort by direct electro-pneumatic control of the spray guns by HMI
- Shorter cleaning times by optimized exhaust performance
- Height adjustable and horizontally moveable control panel
- Combinations with different internal coating drier options (1,2 or 3 rows)
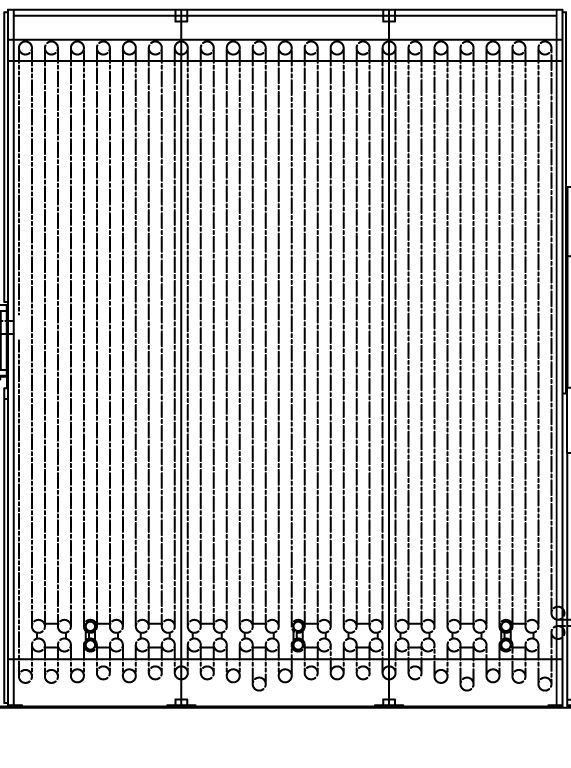
Accumulator 1
for accumulating the cylinders and compensating the asynchronous operation of the washing machine and internal coating machine.
Special features
- Three-part welded frame, mounted onto the floor with a capacity of 2000 cans
- Constant chain tension system
- Connecting traverse at accumulator outfeed to bridge a walkway
- Safety covering of the accumulator up to a height of 2,5 m with acrylic glass panes at the front side, rear and top with sheet metal covering. A complete covering of the accumulator is optionally available
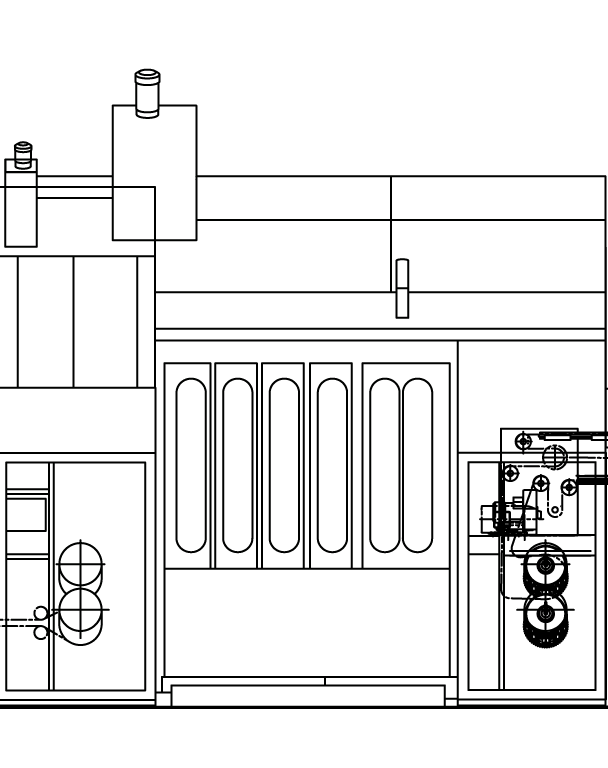
Washing machine
After pressing and trimming it is necessary to wash the lubricants from the cylinders. With our space-saving washing machines, designed in stainless steel, we offer an economic and energy-saving technology for a perfect washing result. Different machine types and a lot of special features allow as much customization as possible.
Technical data
Type | CWM 45-5+ | CWM 55-5+ | CWM 66-5+ |
---|---|---|---|
Diameter range (mm) | 20-45 | 35-55 | 45-66 |
Chain pitch | 3 x ¾” | 4 x ¾” | 5 x ¾” |
Number of washing / rinsing cabins | 5 | 5 | 5 |
Special features
- Compact, space-saving stainless steel design, washing and rinsing cabins equipped with windows
- Reliable, adaptable infeed and outfeed system ensuring easy connection to the upstream and downstream machines
- Safe and reliable infeed and outfeed transfer through vacuum drums
- Gas or electrically heated stainless-steel drying oven with long dwell time and minimum energy consumption
- Newly designed jet spray system
- Detergent dosing by means of conductivity metering and dosing pump
- Dripping area between wet and dry zone, vertically arranged pins
- Electrically heated tanks for the degreasing cabins equipped with pumps, level control and temperature control
- Automatic level control of the tanks, equipped with a safety unit against water shortage and temperature monitoring unit
- Stainless steel tanks for collecting the dripping water below the machine
- Reliable system for sucking off the oven exhaust air
- New extra platform on top of the washing cabins for a better accessibility of the dryer
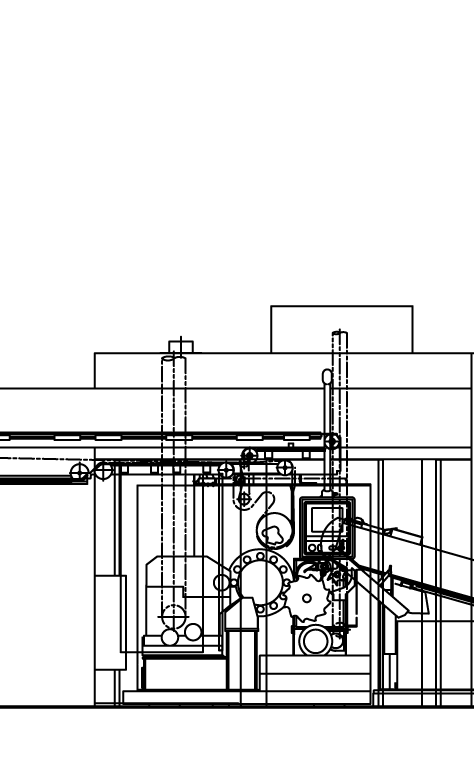
Trimming machine
The high-performance trimming machines, designed for trimming aluminium preforms to length and for brushing the body, have been fully equipped to allow flawless integration into automatic production lines. When designing the machine, particular importance was attached to ease of operation, quick tool change, easy access, solid process technology, high operational safety and little maintenance.
Technical data
Type | MHB | MHB-G | SBB | SBM (without brushing) |
---|---|---|---|---|
Can diameter (mm) | 35-66 | 35-80 | 22-66 | 22-66 |
Max. extruded overall length (mm) | 275 | 295 | 285 | 285 |
Max. trimmed can length(mm) | 260 | 280 | 270 | 270 |
Assumed wall thickness of cans (mm) | 0,2 - 0,6 | 0,2 - 1,0 | 0,35 - 0,8 | 0,35 - 0,8 |
Special features:
- Fully accessible from the front (MHB series), perfect control of all movements, easy change of the brush
- Centralized lubricating system
- The trimming system produces burrless cuts and guarantees a long tool life, precision adjustment in both axial and radial direction
- Mandrel quick-change systems
- Can scrap will be shredded into small pieces for easy suckoff
- Equipment for the separation and safe discharge of the trimming scrap
- Size parts are immediately located in the correct position
- The drum-type transfer unit makes sure the cylinders are safely transferred to the downstream equipment
- Continuously operating conveyor chain at the transfer station (MHB series)
- Deactivation of the oscillating movement of the grinding wheels possible (MHB)
- Automatic and smooth brush cleaning unit with adjustable cleaning cycle and use of commercial grinding wheels (MHB)
- Newly designed compact brushing unit for improved ergonomics, easier changeovers and maintenance (MHB)
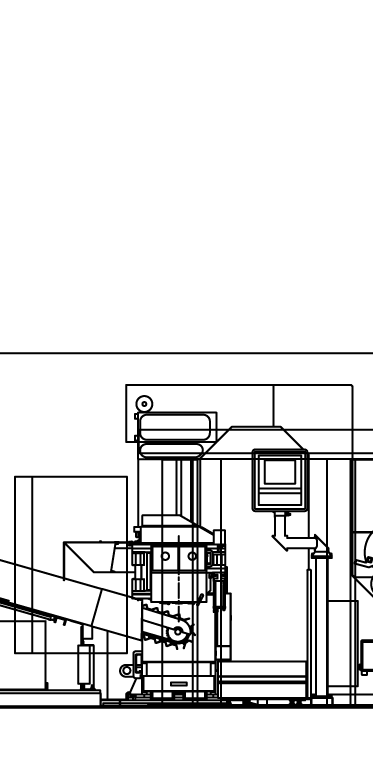
Ironing machine
The cylinder wall thickness is optimized and the bottom is formed. This leads to constant geometrical features and light weight bottles.
Special features
- Transfer of the cylinders from the outfeed conveyor of the impact extrusion press to the tray-type conveyor of the ironing press
- Punches with two punch holders
- Ironing rings and stripper exchangeable from above
- Pneumatically operated bottom forming unit with two dies, swing-off type
- Quick lock for facilitating punch and die exchange
- Electrical punch heating for temperature control of the punches
- Transfer of the cylinders to the synchronous transfer of the trimming machine
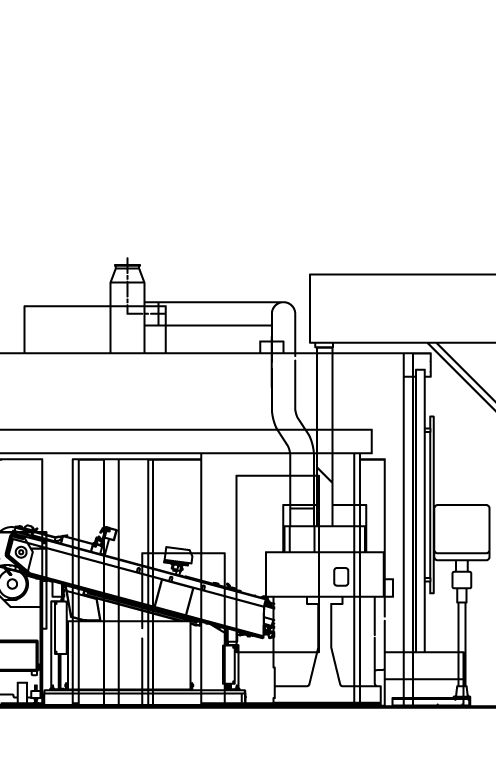
Press
If flexibility is required when producing a monoblock aluminium container, an Impact Extrusion Press is the first choice. A high performance toggle lever system produces aluminium cylinders with one stroke out of a slug. As a market leader, our presses are used all over the world for the production of aluminium bottles.
Technical data
Type | CP35 | CP55 | CP65 | CP75 | CP85 | Express 6000 |
---|---|---|---|---|---|---|
Can diameter (mm) | 10-30 | 19-45 | 25-45 | 25-53 | 35-66 | 43-80 |
Max. extruded can length (mm) | 130 | 170 | 200 | 225 | 275 | 310 |
Approx. wall thickness (mm) | 0,3 | 0,3 | 0,4 | 0,5 | 0,5 | 1,0 |
Nominal press force (kN) | 800 | 1.400 | 1.600 | 2.500 | 4.000 | 6.000 |
Special features
- Sturdy frame, separate from the drive housing, for absorbing the extrusion loads; both parts made of spheroidal graphite iron
- Compact drive of the crankshaft via pneumatically controlled clutch-brake unit with spring loaded disc brake to allow controlled or immediate stops
- Speed-variable drive, creeping speed and facility for switching to reverse motion to facilitate the setting of the tooling
- Electromotive punch adjustment for correcting the bottom thickness during production
- Swing-off type slug feed and stripper frame of the take-off unit, resulting in short set-up times and simple size-part changes, optimized for high speed production
- Automatic permanent circulatory lubrication system with filter and offline filter system
- Take-off unit operating in absolute synchronism with the outfeed conveyor, ensuring trouble-free transfer of the products even in case of short extrusions and maximum stroke rates
- Inclined slug conveyor for direct feed of flat and domed slugs to the die
- Continuous rotary slug infeed system
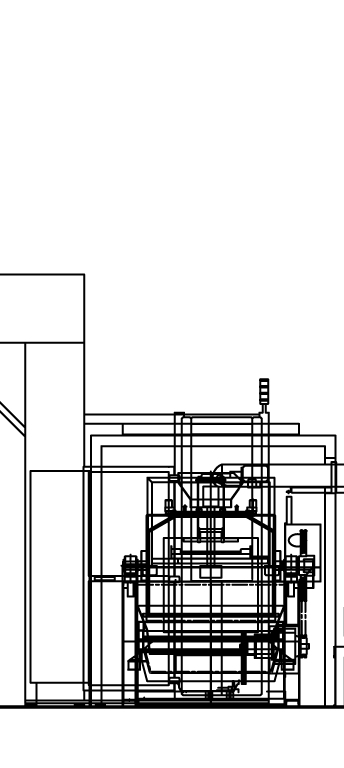
Slug infeed
In the sorting and feeding unit the slugs are separated, aligned and fed into the extrusion press.
The processing of flat or domed slugs is possible.
Special features
- Storage container with inner lining to avoid damaged slugs
- Level control of the container by means of ultrasonic sensor
- Plate type conveyor belt
- Possibility to regulate the speed of the conveyor belt for different slug sizes
- Feed chute to the clamping-type elevator
- Clamping-type slug elevator, with overload protection at the transfer of the feed chute
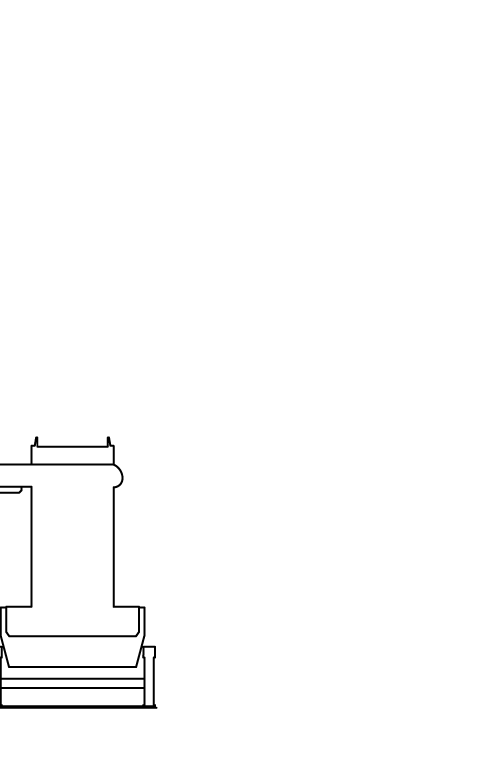
Slug lubrication
The aluminium slugs are lubricated and transported to the sorting and feeding unit.
Special features
- Storage bin for storing slugs for one lubricating process
- Feeding of slugs to the lubricating barrel by means of conveyor belt
- Abrasion-proof lining of the barrel body with cover
- Manually assisted cover lifting device, monitored by limit switches
- Elevator-type conveyor belt for transporting the slugs
CMX
The new CMX Impact Extrusion line of mall//herlan with a production speed of up to 250 cpm exceeds limits. The machine technology to produce shaped aluminium bottles at this speed is unrivalled worldwide. The increase of speed has been made possible for example by new transfer units and the optimisation of infeed drums in the front-end and decoration area. Even the production of shaped bottles is possible at a speed of 250 cpm with our 40 station or even bigger necking systems.
Packing machine
for strapping aluminium bottles in bundles or layer blocks for pallet packing
Special features
- Ideal for aluminium bottles
- Optimal grouping of bottles
- Fast and gentle strapping via servo-controlled process
- Synchronous bottle transport from the upstream machine
- High production reliability and security
- Supplement machine to palletize the bundles are available
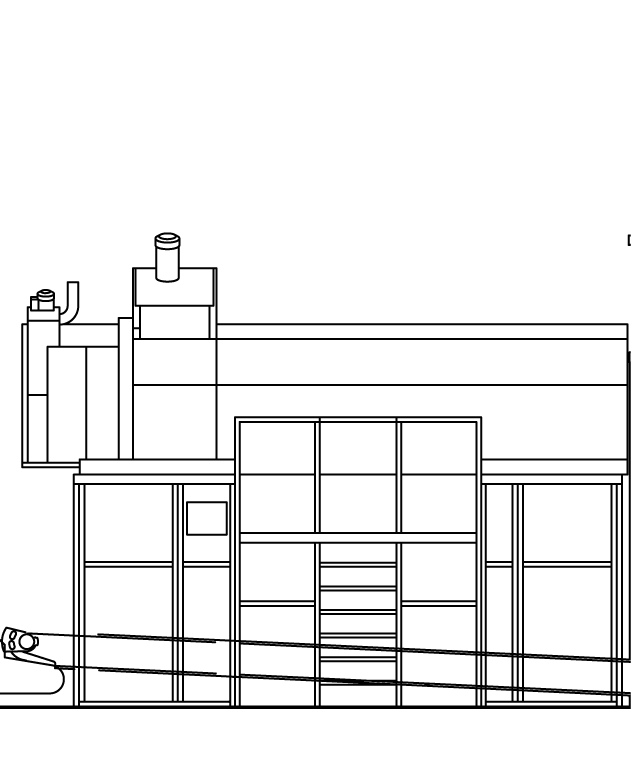
Postwasher
Our customized postwashing machines are equipped with a patented spraying system to ensure low water consumption.
A bypass function for the transport without washing/rinsing is included as standard.
Technical data
Type | PWMx 45 | PWMx 55 | PWMx 66 |
---|---|---|---|
Max. Diameter (mm) | 45 | 55 | 66 |
Chain pitch | 3 x ¾” | 4 x ¾” | 5 x ¾” |
Number of washing / rinsing cabins | 2 | 2 | 2 |
Special features
- Stainless steel design, cabins equipped with windows
- Washing of the bottles in the first washing/rinsing cabin
- Rinsing of the bottles in the following rinsing cabins
- All cabins equipped with a patented spraying system with low water consumption
- Electrically heated tank for the first washing/rinsing cabin equipped with pumps, level control and temperature regulation
- Dripping area after washing, vertically arranged pins and drying blades
- Automatic level control of the tanks, equipped with safety unit against water shortage, temperature monitoring unit
- Stainless steel tank for collecting the dripping water below the washing machine
- Drying of the bottles in the gas heated oven, low-energy design
- Chain guides made of PTFE (Teflon)
- Additional blowing nozzles for drying the interior and the rim of the bottles
- Reliable system for sucking off the oven exhaust air
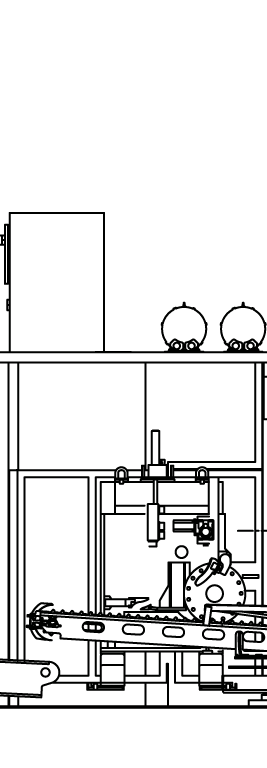
Leak detector
A photocell is used to detect if rays of light fall into the bottle through micro-holes. Defective bottles are automatically ejected at the outfeed conveyor after the Leak detector. A 100% quality-control ensures that only complete secure bottles leave the line.
The Leak detector can be placed on the outfeed conveyor of the Necking machine. Alternatively it can be integrated as a stand-alone machine in the line.
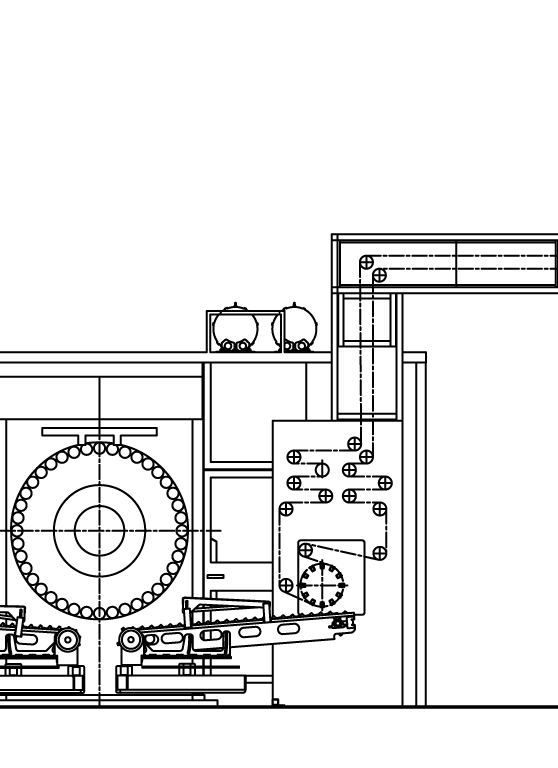
Necking machine
The cylinder is necked and shaped by necking dies up to the final bottle design. Processes as threading, curling, beading, registered embossing and debossing to create unique shapes and designs fitting the needs of your customers.
Technical data
Type | C250.40VE |
---|---|
Can diameter (mm) | 35 - 66 |
Finished product length (mm after necking) | 105 - 250 |
Number of stations | 40 |
Total stroke (mm) | 110 - 270 |
Usable stroke (mm) | 86 - 202 |
Special features
- Pneumatic holding grippers with electronic control for bottle detection guarantee a constant stable position of the bottle
- Tool quick-change system for maximum product flexibility
- Compressed air-assisted necking to enable even complicated shapes
- Bottom forming unit included in the standard supply
- Maximum accessibility to the machine working area for easy handling and setting of the tools
- Optimized bottle transfer systems between conveyors and drums
- Infinitely adjustable stroke
- Electronic presetting device to set lubrication cycle frequency
- Possible application of all our proprietary tools allowing wide machining possibilities
- Frequency-controlled motors for rotating tools
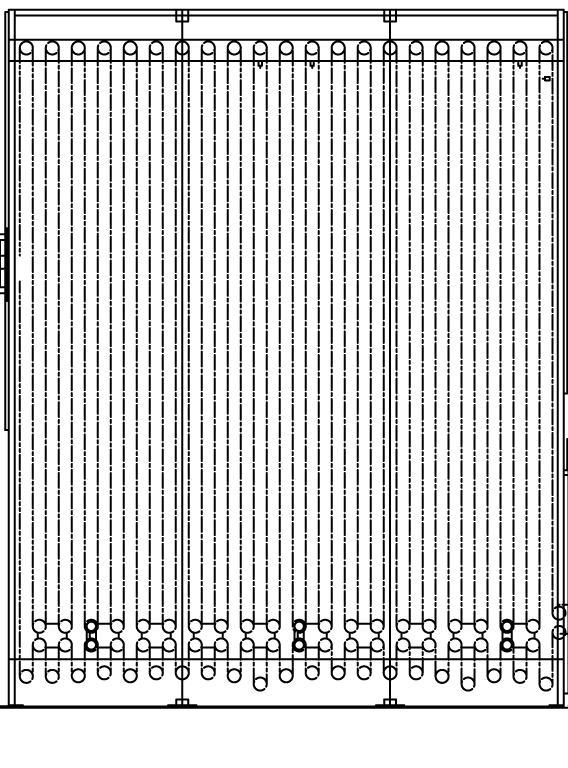
Accumulator 3
for accumulating the cylinders and compensating the asynchronous operation of decoration unit and necking machine.
Special features
- Two-part welded frame, mounted onto the floor
- Constant chain tension system
- Safety covering of the accumulator up to a height of 2,5 m with acrylic glass panes at the front side, rear and top with sheet metal covering. A complete covering of the accumulator is optionally available
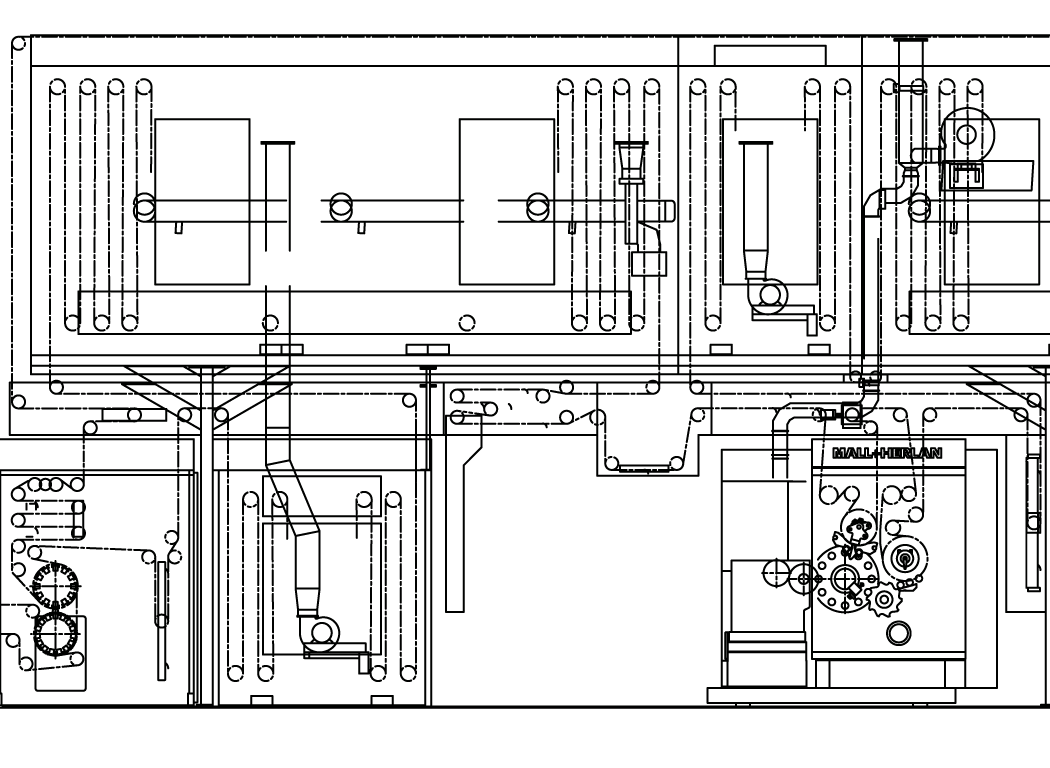
Overvarnish lacquering machine
The overvarnish is applied to protect the decoration. According to the request of your customers also special effects like matt, semi matt, gloss or haptic can be provided.
Special features
- Cylinder transfer from the conveyor chain to a mechanical take-off drum with size-independent vacuum pockets
- Mechanical indexing gear unit with 12 stations
- Mandrel quick change unit and monitoring of the correct clamping
- Infinitely variable mandrel drive by means of controlled servomotor
- Vacuum-assisted loading and steadying of the cylinders on the mandrels, before and during processing
- Three roller base-coating unit designed as V-type-coating unit
- Transfer unit with take-off control and two suction units for transporting the cylinders from the mandrels onto the chain pins
- Oven chamber with integrated chain guide
- Sprocket bearings with re-lubricating facility, installed outside the oven in an aluminium casing sealed towards the rear wall of the oven
- Possibility of cylinder sampling for test purposes from the pins of the dryer chain, after drying of the clear varnish.
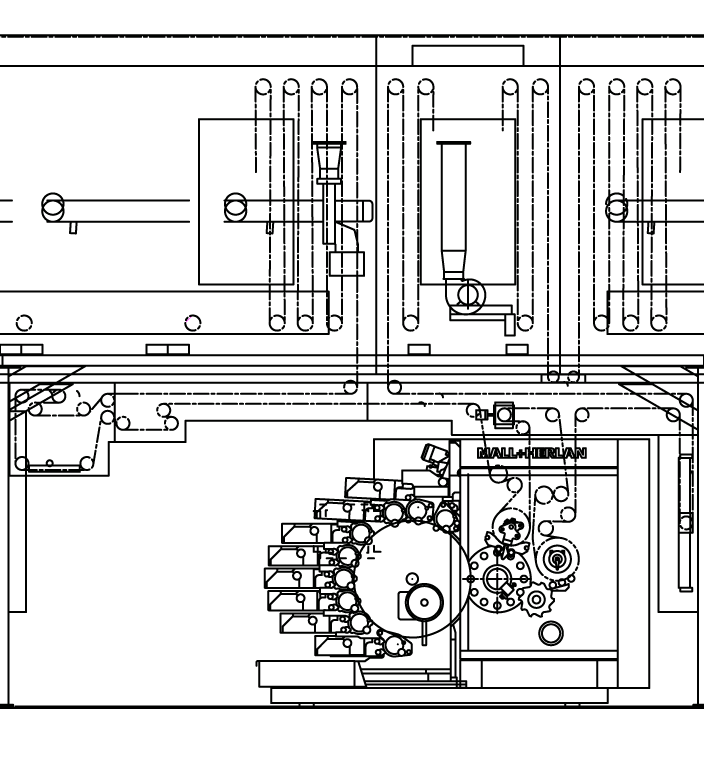
Printing machine
The printing unit, which can apply up to 9 colours, ensures the widest possible decoration variety for aluminium bottles
Special features
- Cylinder transfer from the conveyor chain to a mechanical take-off drum with size-independent vacuum pockets
- Mechanical indexing gear unit with 12 stations
- Mandrel quick change unit and monitoring of the correct clamping
- Infinitely variable mandrel drive by means of controlled servomotor
- Vacuum-assisted loading and steadying of the cylinders on the mandrels, before and during processing
- Printing unit with up to 9 colours
- Transfer unit with take-off control and two suction units for transporting the cylinder from the mandrels onto the chain pins
- Oven chamber with integrated chain guide
- Sprocket bearings with re-lubricating facility, installed outside the oven in an aluminium casing sealed towards the rear wall of the oven
- Possibility of cylinder sampling for test purposes from the pins of the dryer chain, after drying of the printing inks.
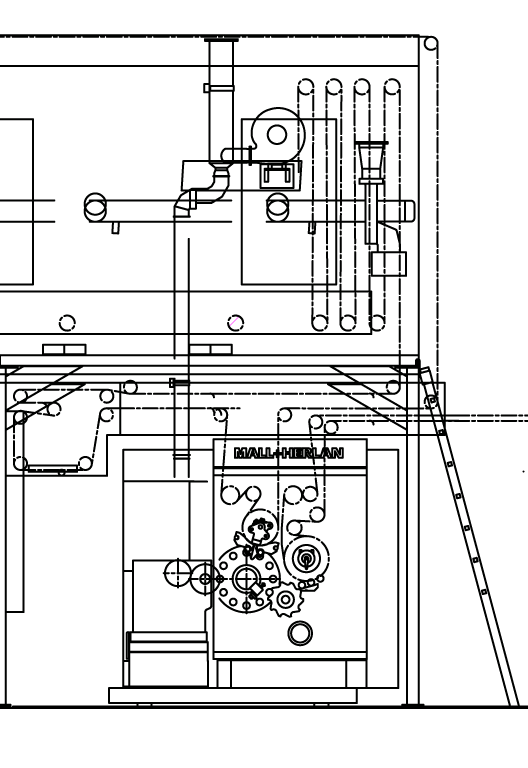
Basecoat lacquering machine
The cylinder receives the base coat which is important for the stain resistance and excellent print quality. The base coat is dried in the first oven chamber of the decoration drying oven.
Special features
- Cylinder transfer from the conveyor chain to a mechanical take-off drum with size-independent vacuum pockets
- Mechanical indexing gear unit with 12 stations
- Mandrel quick change unit and monitoring of the correct clamping
- Infinitely variable mandrel drive by means of controlled servomotor
- Vacuum-assisted loading and steadying of the cylinder on the mandrels, before and during processing
- Three roller base-coating unit designed as V-type-coating unit
- Transfer unit with take-off control and two suction units for transporting the cylinders from the mandrels onto the chain pins
- Oven chamber with integrated chain guide
- Sprocket bearings with re-lubricating facility, installed outside the oven in an aluminium casing sealed towards the rear wall of the oven
- Possibility of cylinder sampling for test purposes from the pins of the dryer chain, after drying of the basecoat
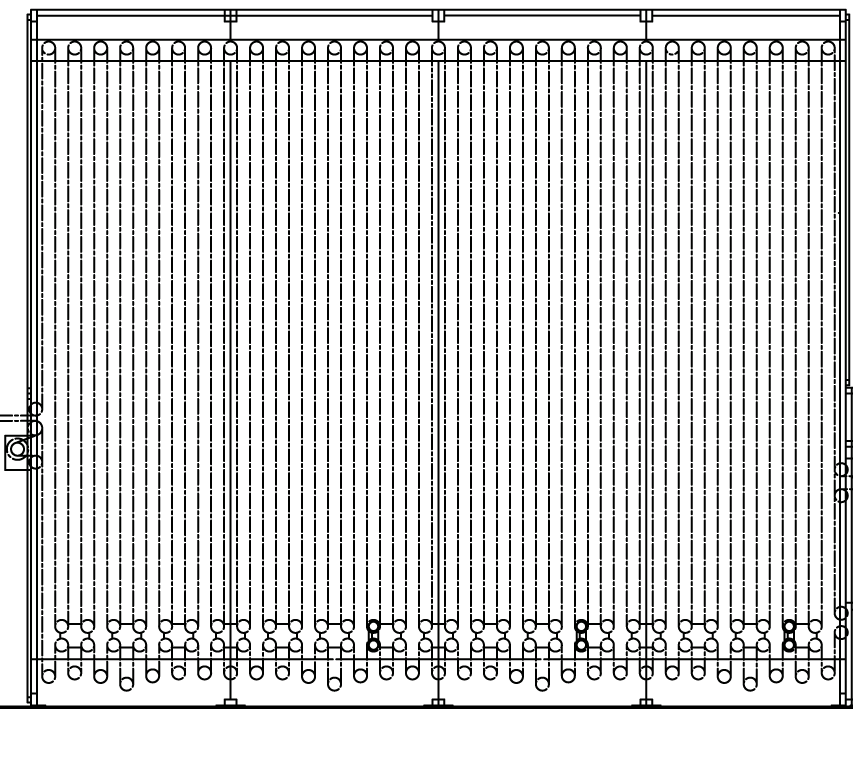
Accumulator 2
for accumulating the cylinders and compensating the asynchronous operation of internal coating machine and decoration unit.
Special features
- Four-part welded frame, mounted onto the floor
- Constant chain tension system
- Safety covering of the accumulator up to a height of 2,5 m with acrylic glass panes at the front side, rear and top with sheet metal covering. A complete covering of the accumulator is optionally available
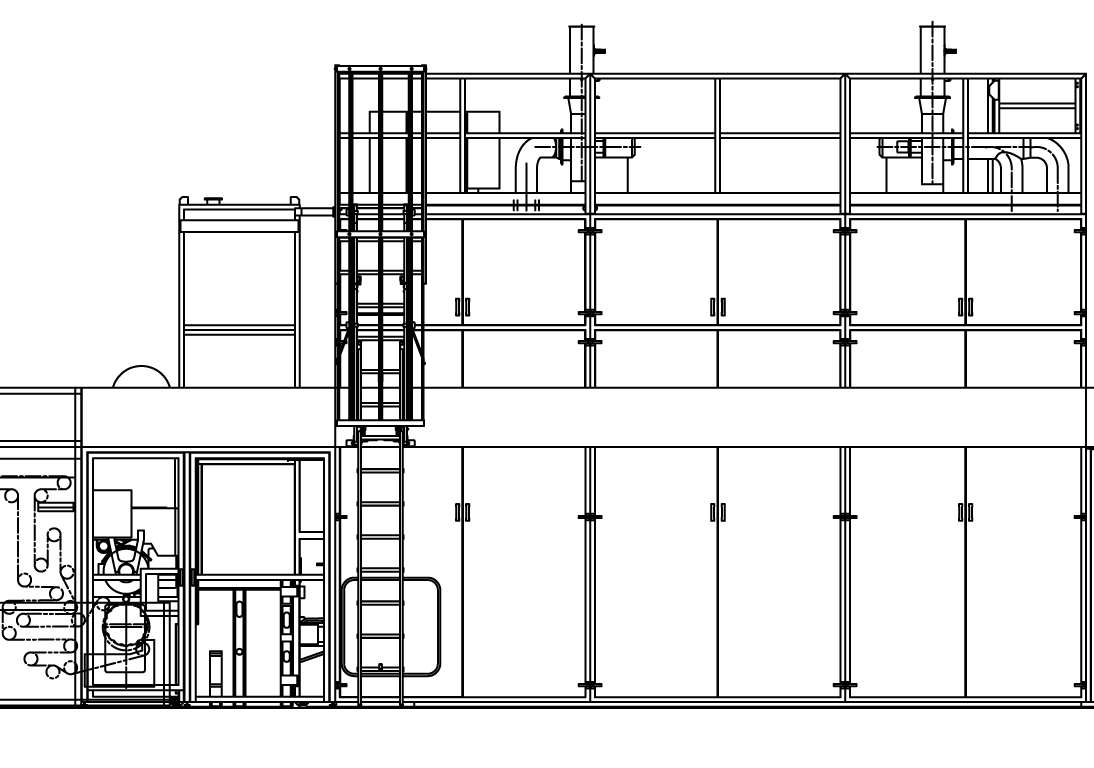
Internal coat dryer
for polymerizing the internal lacquer coat, electrically heated or alternatively by gas.
Special features
- 1,2 or 3 row transport chain with baskets
- Reduced wear-out of the transport chain and the chain wheels by cardan-based drive system
- Chain tension with weight, electronically monitored
- Easy accessibility to the dryer interior due to large doors
- Quadruple door look
- Isolated doors with special door hinges for synchronized door closing
- Large outer doors with smooth surface on the oven’s front and rear sides
- Quick and easy removal and reassembly of the shafts and chain wheels in case of service
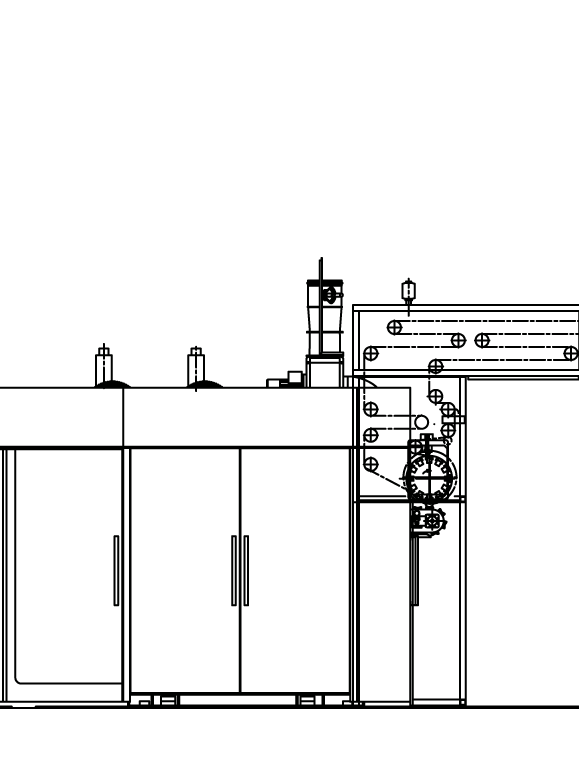
Internal coating machine
A functional lacquer is applied to seal the inside of the cylinder using moveable spray lances. In the following oven with its cooling zone the inside lacquer is cured and hardened.
Special features
- Low vibration due to solid mechanical design
- Individual vacuum circuit for machine infeed and outfeed
- Increased user comfort by direct electro-pneumatic control of the spray guns by HMI
- Shorter cleaning times by optimized exhaust performance
- Height adjustable and horizontally moveable control panel
- Combinations with different internal coating drier options (1,2 or 3 rows)
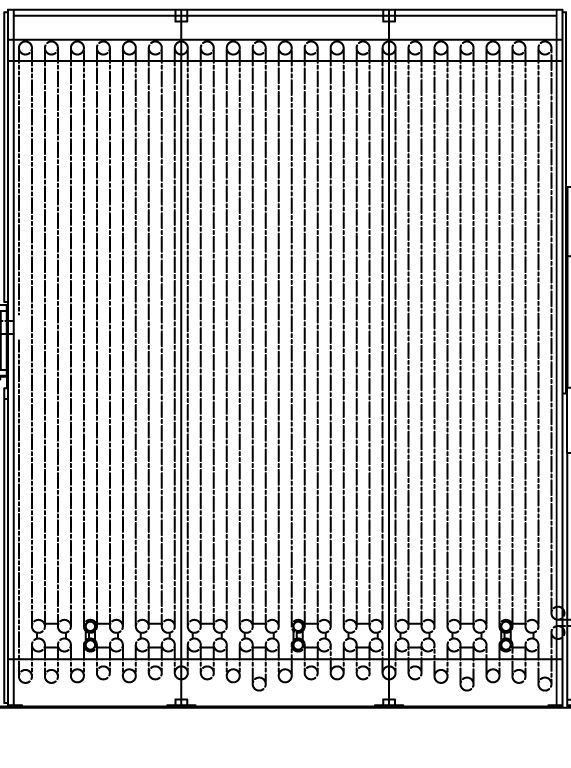
Accumulator 1
for accumulating the cylinders and compensating the asynchronous operation of the washing machine and internal coating machine.
Special features
- Three-part welded frame, mounted onto the floor
- Constant chain tension system
- Connecting traverse at accumulator outfeed to bridge a walkway
- Safety covering of the accumulator up to a height of 2,5 m with acrylic glass panes at the front side, rear and top with sheet metal covering. A complete covering of the accumulator is optionally available
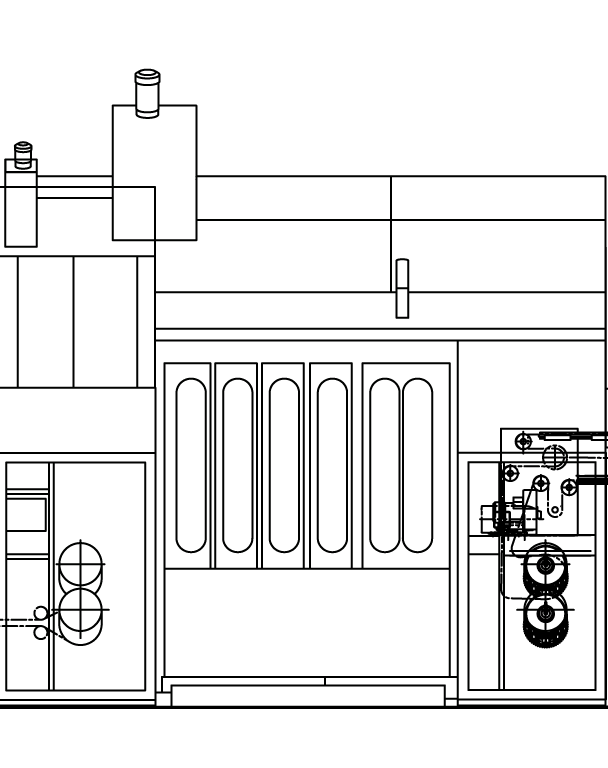
Washing machine
After pressing and trimming it is necessary to wash the lubricants from the cylinders. With our space-saving washing machines, designed in stainless steel, we offer an economic and energy-saving technology for a perfect washing result. A lot of special features allow as much customization as possible.
Technical data
Type | CWMx 59-5+ | CWMx 66-8 |
---|---|---|
Diameter range (mm) | 35-59 | 45-66 |
Chain pitch | 4 x ¾” | 5 x ¾” |
Number of washing / rinsing cabins | 5 | 8 |
Special features
- Compact, space-saving stainless steel design, washing and rinsing cabins equipped with windows
- Reliable, adaptable infeed and outfeed system ensuring easy connection to the upstream and downstream machines
- Safe and reliable infeed and outfeed transfer through vacuum drums
- Gas or electrically heated stainless-steel drying oven with long dwell time and minimum energy consumption
- Newly designed jet spray system
- Detergent dosing by means of conductivity metering and dosing pump
- Dripping area between wet and dry zone, vertically arranged pins
- Electrically heated tanks for the degreasing cabins equipped with pumps, level control and temperature control
- Automatic level control of the tanks, equipped with a safety unit against water shortage and temperature monitoring unit
- Stainless steel tanks for collecting the dripping water below the machine
- Reliable system for sucking off the oven exhaust air
- New extra platform on top of the washing cabins for a better accessibility of the dryer
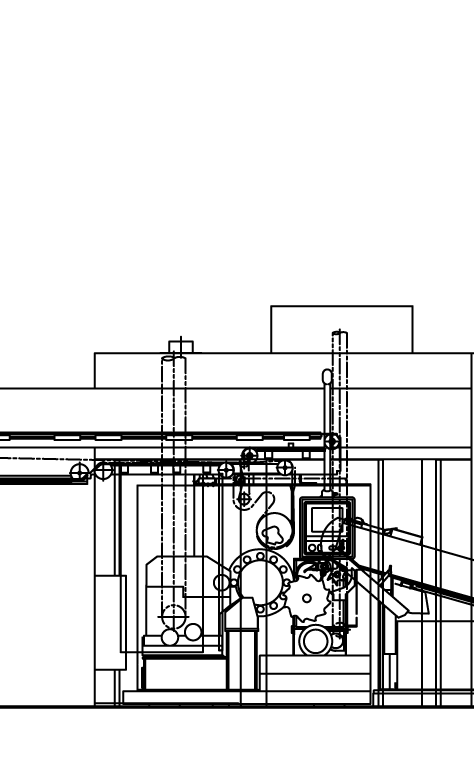
Trimming machine
The high-performance trimming machines, designed for trimming aluminium preforms to length and for brushing the body, have been fully equipped to allow flawless integration into automatic production lines. When designing the machine, particular importance was attached to ease of operation, quick tool change, easy access, solid process technology, high operational safety and little maintenance.
Technical data
Type | MHBx |
---|---|
Can diameter (mm) | 35 - 66 |
Max. extruded overall length (mm) | 275 |
Max. trimmed can length(mm) | 260 |
Assumed wall thickness of cans (mm) | 0,2 - 0,6 |
Special features:
- Fully accessible from the front, perfect control of all movements, easy change of the brush
- Centralized lubricating system
- The trimming system produces burr less cuts and guarantees a long tool life, precision adjustment in both axial and radial direction
- Mandrel quick-change systems
- Can scrap will be shredded into small pieces for easy suckoff
- Equipment for the separation and safe discharge of the trimming scrap
- Size parts are immediately located in the correct position
- The drum-type transfer unit makes sure the cylinders are safely transferred to the downstream equipment
- Continuously operating conveyor chain at the transfer station
- Deactivation of the oscillating movement of the grinding wheels possible
- Automatic and smooth brush cleaning unit with adjustable cleaning cycle and use of commercial grinding wheels
- Newly designed compact brushing unit for improved ergonomics, easier changeovers and maintenance
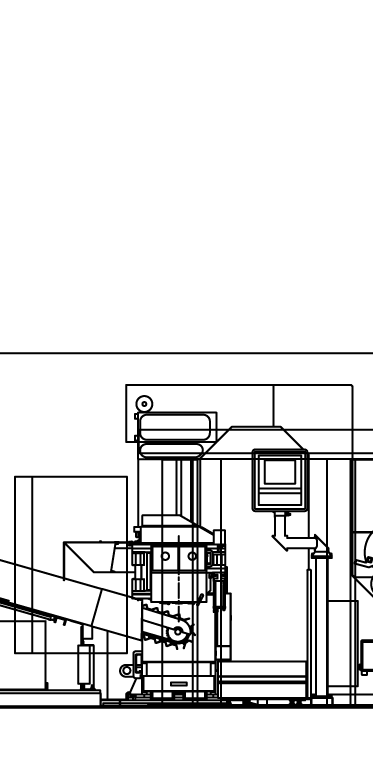
Ironing machine
The cylinder wall thickness is optimized and the bottom is formed. This leads to constant geometrical features and light weight bottles.
Special features
- Transfer of the cylinders from the outfeed conveyor of the impact extrusion - press to the tray-type conveyor of the ironing press
- Punches with two punch holders
- Ironing rings and stripper exchangeable from above
- Pneumatically operated bottom forming unit with two dies, swing-off type
- Quick lock for facilitating punch and die exchange
- Electrical punch heating for temperature control of the punches
- Transfer of the cylinders to the synchronous transfer of the trimming machine
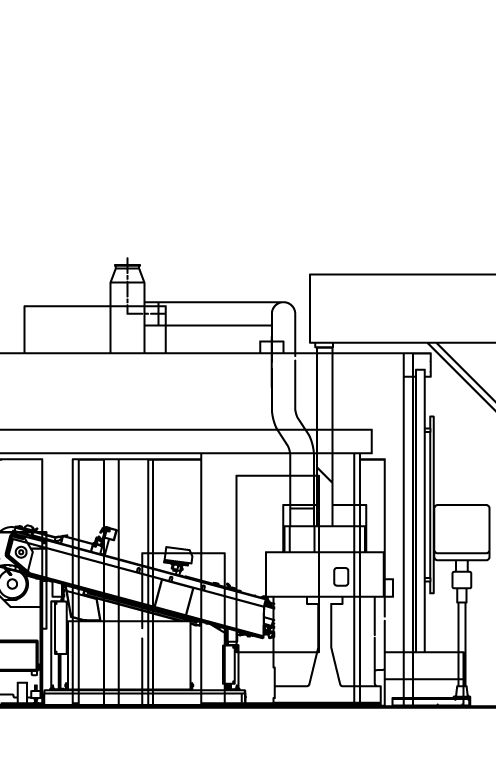
Press
If flexibility is required when producing a monoblock aluminium container, an Impact Extrusion Press is the first choice. A high performance toggle lever system produces aluminium cylinders with one stroke out of a slug. As a market leader, our presses are used all over the world for the production of aluminium bottles.
Technical data
Type | Express 4000 |
---|---|
Can diameter (mm) | 35-66 |
Max. extruded can length (mm) | 275 |
Approx. wall thickness (mm) | 0,5 |
Nominal press force (kN) | 4.000 |
Special features
- Sturdy frame, separate from the drive housing, for absorbing the extrusion loads; both parts made of spheroidal graphite iron
- Compact drive of the crankshaft via pneumatically controlled clutch-brake unit with spring loaded disc brake to allow controlled or immediate stops
- Speed-variable drive, creeping speed and facility for switching to reverse motion to facilitate the setting of the tooling
- Electromotive punch adjustment for correcting the bottom thickness during production
- Swing-off type slug feed and stripper frame of the take-off unit, resulting in short set-up times and simple size-part changes, optimized for high speed production
- Automatic permanent circulatory lubrication system with filter and offline filter system
- Take-off unit operating in absolute synchronism with the outfeed conveyor, ensuring trouble-free transfer of the products even in case of short extrusions and maximum stroke rates
- Inclined slug conveyor for direct feed of flat and domed slugs to the die
- Continuous rotary slug infeed system
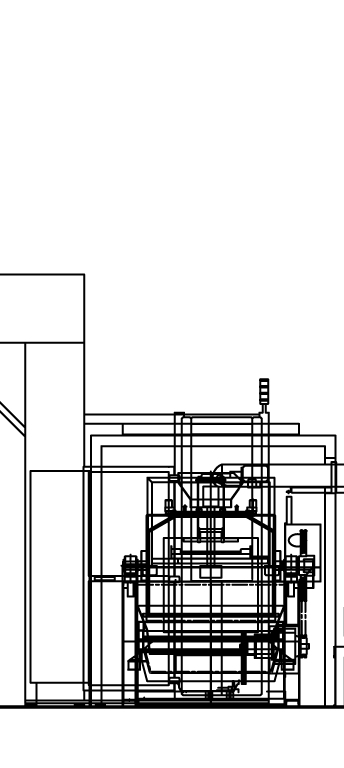
Slug infeed
In the sorting and feeding unit the slugs are separated, aligned and fed into the extrusion press. The processing of flat or domed slugs is possible.
Special features
- Storage container with inner lining to avoid damaged slugs
- Level control of the container by means of ultrasonic sensor
- Plate type conveyor belt
- Possibility to regulate the speed of the conveyor belt for different slug sizes
- Feed chute to the clamping-type elevator
- Clamping-type slug elevator, with overload protection at the transfer of the feed chute
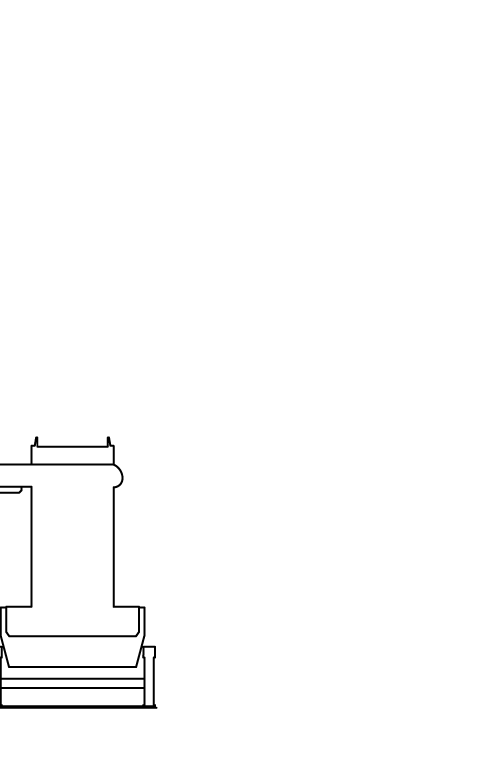
Slug lubrication
The aluminium slugs are lubricated and transported to the sorting and feeding unit.
Special features
- Storage bin for storing slugs for one lubricating process
- Feeding of slugs to the lubricating barrel by means of conveyor belt
- Abrasion-proof lining of the barrel body with cover
- Manually assisted cover lifting device, monitored by limit switches
- Elevator-type conveyor belt for transporting the slugs
CMC180G
This line is your choice for bottles with a bigger diameter and/or greater length.
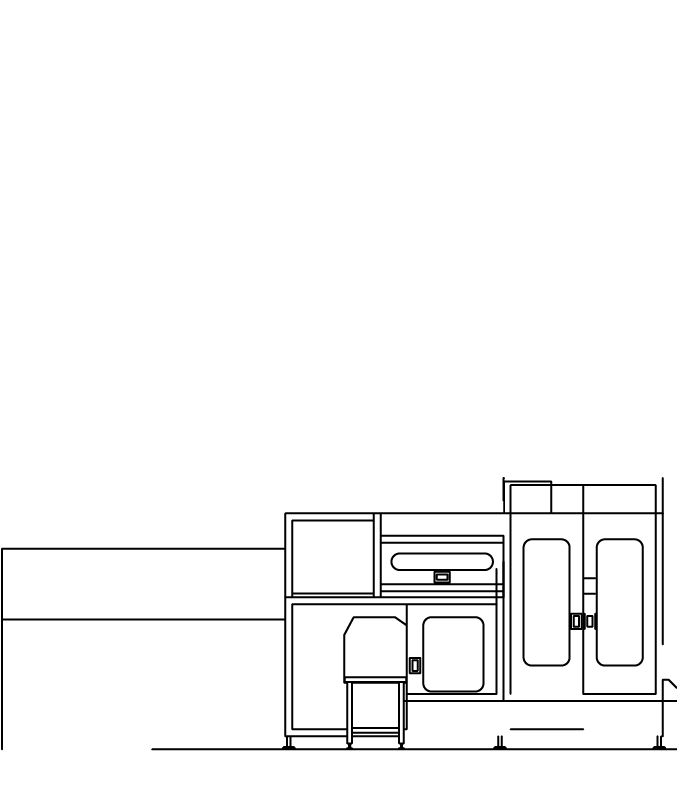
Packing machine
for strapping aluminium bottles in bundles or layer blocks for pallet packing
Special features
- Ideal for aluminium bottles
- Optimal grouping of bottles
- Fast and gentle strapping via servo-controlled process
- Synchronous bottle transport from the upstream machine
- High production reliability and security
- Supplement machine to palletize the bundles are available
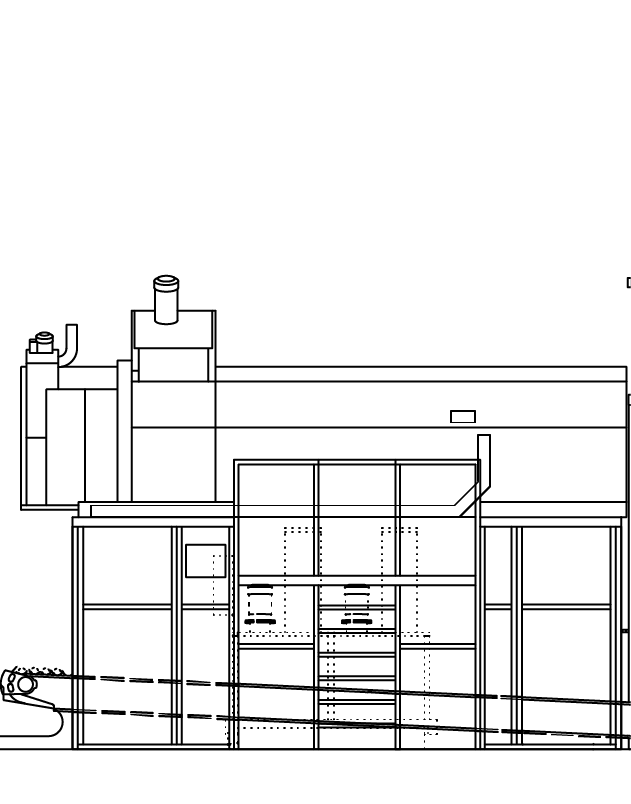
Postwasher
Our customized postwashing machines are equipped with a patented spraying system to ensure low water consumption.
A bypass function for the transport without washing/rinsing is included as standard.
Technical data
Type | PWM 80 |
---|---|
Max. Diameter (mm) | 80 |
Chain pitch | 6 x ¾” |
Number of washing / rinsing cabins | 2 |
Special features
- Stainless steel design, cabins equipped with windows
- Washing of the bottles in the first washing/rinsing cabin
- Rinsing of the bottles in the following rinsing cabins
- All cabins equipped with a patented spraying system with low water consumption
- Electrically heated tank for the first washing/rinsing cabin equipped with pumps, level control and temperature regulation
- Dripping area after washing, vertically arranged pins and drying blades
- Automatic level control of the tanks, equipped with safety unit against water shortage, temperature monitoring unit
- Stainless steel tank for collecting the dripping water below the washing machine
- Drying of the bottles in the gas heated oven, low-energy design
- Chain guides made of PTFE (Teflon)
- Additional blowing nozzles for drying the interior and the rim of the bottles
- Reliable system for sucking off the oven exhaust air
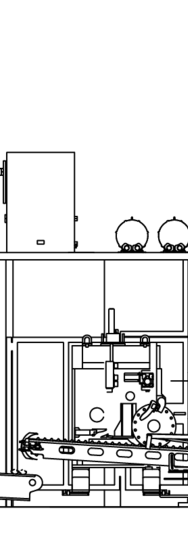
Leak detector
A photocell is used to detect if rays of light fall into the bottle through micro-holes. Defective bottle are automatically ejected at the outfeed conveyor after the Leak detector. A 100% quality-control ensures that only complete secure bottles leave the line.
The Leak detector can be placed on the outfeed conveyor of the Necking machine. Alternatively it can be integrated as a stand-alone machine in the line.
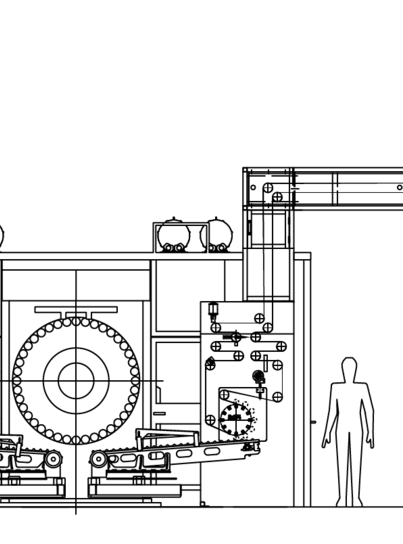
Necking machine
The cylinder is necked and shaped by necking dies up to the final bottle design. Processes as threading, curling, beading, registered embossing and debossing to create unique shapes and designs fitting the needs of your customers.
Technical data
Type | C200.36XVE |
---|---|
Can diameter (mm) | 35-80 |
Finished product length (mm after necking) | 110-275 |
Number of stations | 36 |
Total stroke (mm) | 110 - 270 |
Usable stroke (mm) | 80 - 187 |
Special features
- Pneumatic holding grippers with electronic control for bottle detection guarantee a constant stable position of the bottle
- Tool quick-change system for maximum product flexibility
- Compressed air-assisted necking to enable even complicated shapes
- Bottom forming unit included in the standard supply
- Maximum accessibility to the machine working area for easy handling and setting of the tools
- Optimized bottle transfer systems between conveyors and drums
- Infinitely adjustable stroke
- Electronic presetting device to set lubrication cycle frequency
- Possible application of all our proprietary tools allowing wide machining possibilities
- Frequency-controlled motors for rotating tools
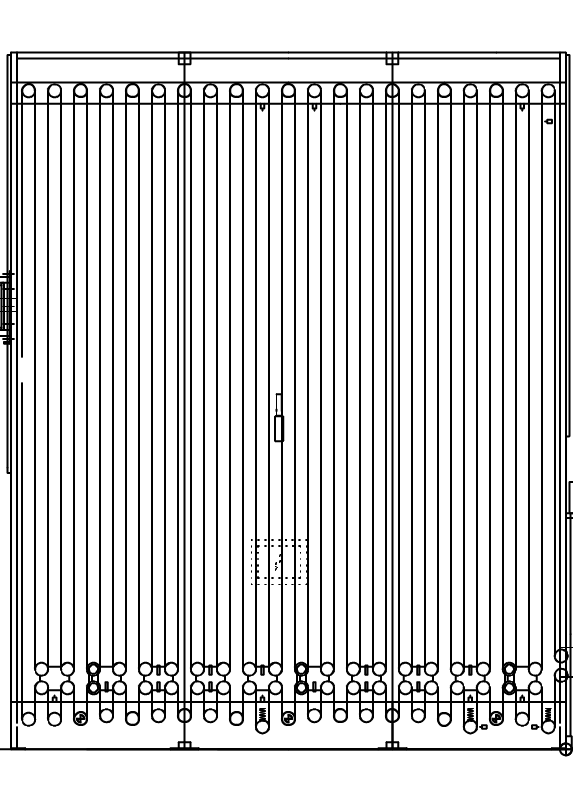
Accumulator 3
for accumulating the cylinders and compensating the asynchronous operation of decoration unit and necking machine.
Special features
- Two-part welded frame, mounted onto the floor with a capacity of 2100 cans
- Constant chain tension system
- Safety covering of the accumulator up to a height of 2,5 m with acrylic glass panes at the front side, rear and top with sheet metal covering. A complete covering of the accumulator is optionally available
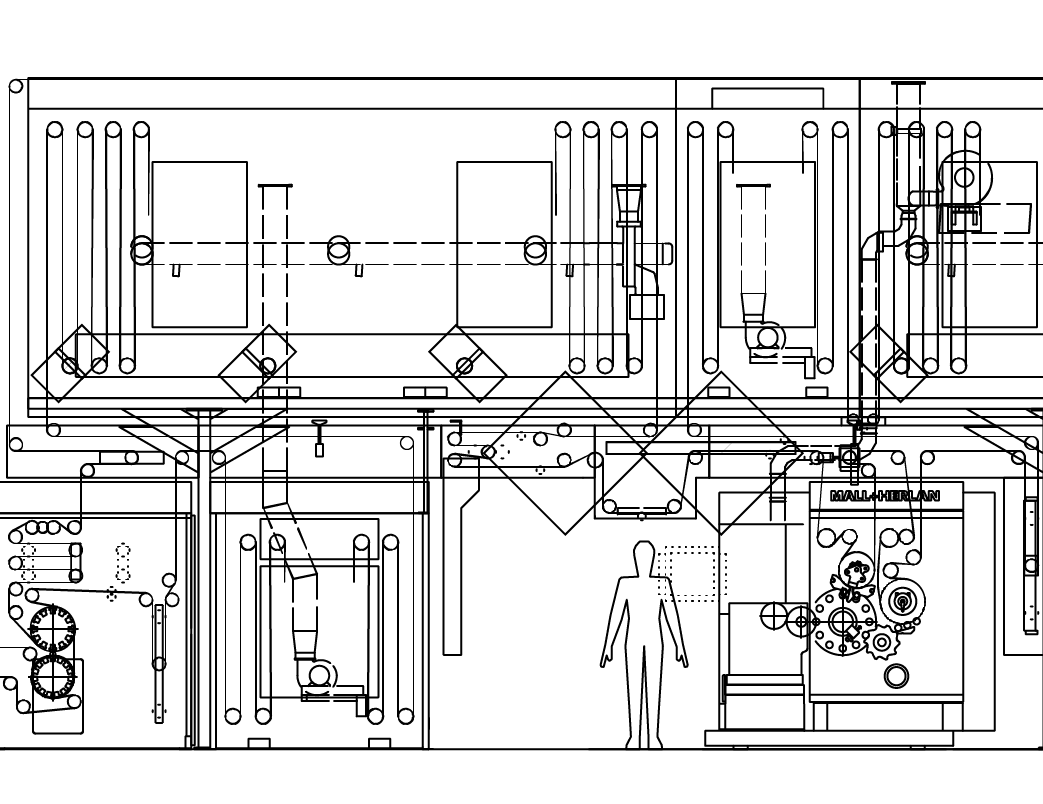
Overvarnish lacquering machine
The overvarnish is applied to protect the decoration. According to the request of your customers also special effects like matt, semi matt, gloss or haptic can be provided.
Special features
- Cylinder transfer from the conveyor chain to a mechanical take-off drum with size-independent vacuum pockets
- Mechanical indexing gear unit with 12 stations
- Mandrel quick change unit and monitoring of the correct clamping
- Infinitely variable mandrel drive by means of controlled servomotor
- Unit for checking whether the cylinder have been correctly loaded on the mandrels
- Vacuum-assisted loading and steadying of the cylinders on the mandrels, before and during processing
- Three roller base-coating unit designed as V-type-coating unit
- Transfer unit with take-off control and two suction units for transporting the cans from the mandrels onto the chain pins
- Oven chamber with integrated chain guide
- Sprocket bearings with re-lubricating facility, installed outside the oven in an aluminium casing sealed towards the rear wall of the oven
- Possibility of cylinder sampling for test purposes from the pins of the dryer chain, after drying of the clear varnish.
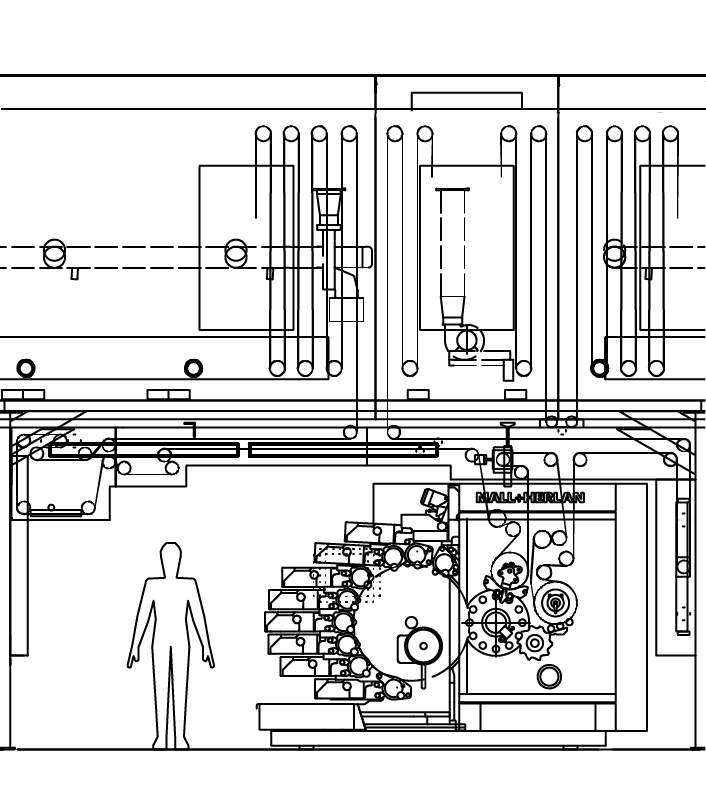
Printing machine
The printing unit, which can apply up to 9 colours, ensures the widest possible decoration variety for aluminium bottles
Special features
- Cylinder transfer from the conveyor chain to a mechanical take-off drum with size-independent vacuum pockets
- Mechanical indexing gear unit with 12 stations
- Mandrel quick change unit and monitoring of the correct clamping
- Infinitely variable mandrel drive by means of controlled servomotor
- Unit for checking whether the cylinders have been correctly loaded on the mandrels
- Printing unit with up to 9 colours
- Transfer unit with take-off control and two suction units for transporting the cylinders from the mandrels onto the chain pins
- Oven chamber with integrated chain guide
- Sprocket bearings with re-lubricating facility, installed outside the oven in an aluminium casing sealed towards the rear wall of the oven
- Possibility of cylinder sampling for test purposes from the pins of the dryer chain, after drying of the printing inks.
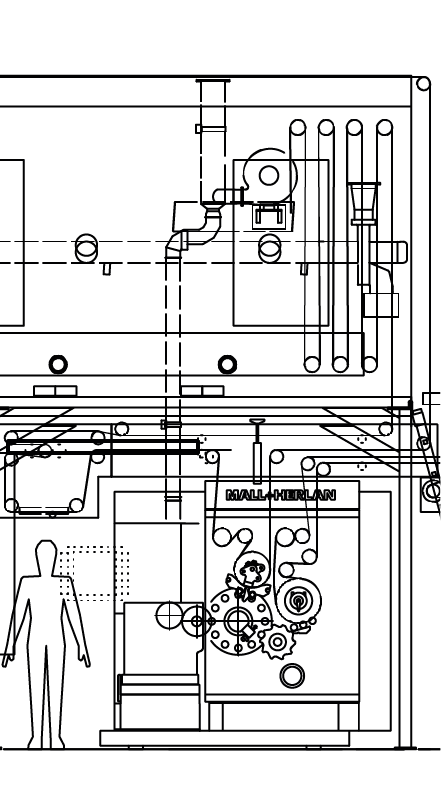
Basecoat lacquering
The cylinder receives the base coat which is important for the stain resistance and excellent print quality. The base coat is dried in the first oven chamber of the decoration drying oven.
Special features
- Cylinder transfer from the conveyor chain to a mechanical take-off drum with size-independent vacuum pockets
- Mechanical indexing gear unit with 12 stations
- Mandrel quick change unit and monitoring of the correct clamping
- Infinitely variable mandrel drive by means of controlled servomotor
- Unit for checking whether the cylinders have been correctly loaded on the mandrels
- Vacuum-assisted loading and steadying of the cylinders on the mandrels, before and during processing
- Three roller base-coating unit designed as V-type-coating unit
- Transfer unit with take-off control and two suction units for transporting the cylinders from the mandrels onto the chain pins
- Oven chamber with integrated chain guide
- Sprocket bearings with re-lubricating facility, installed outside the oven in an aluminium casing with sealed towards the rear wall of the oven
- Possibility of cylinder sampling for test purposes from the pins of the dryer chain, after drying of the basecoat
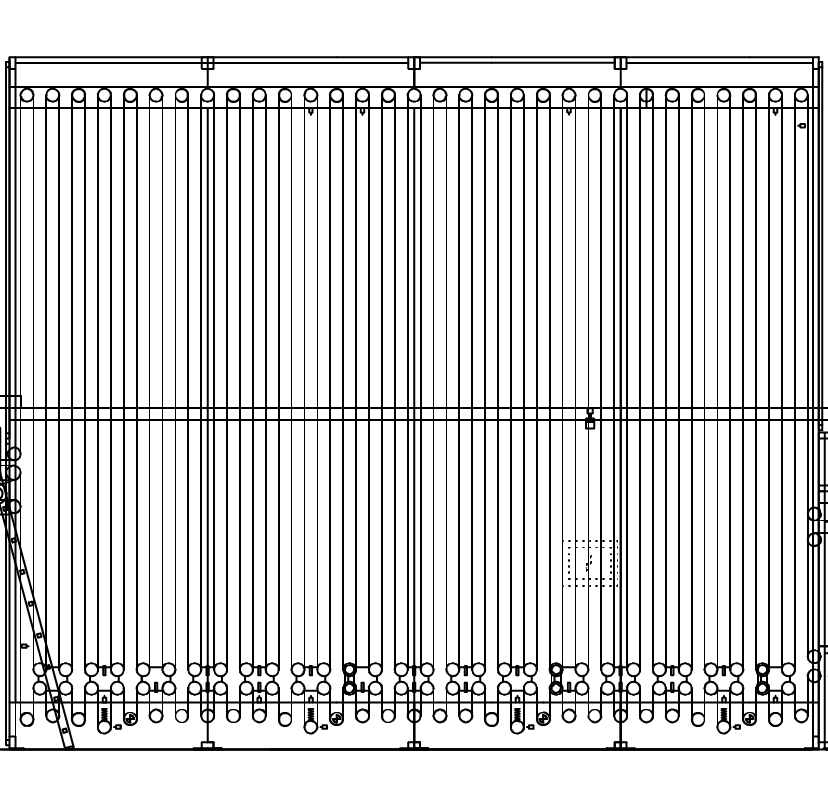
Accumulator 2
for accumulating the cylinders and compensating the asynchronous operation of internal coating machine and decoration unit.
Special features
- Four-part welded frame, mounted onto the floor with a capacity of 3300 cans
- Constant chain tension system
- Safety covering of the accumulator up to a height of 2,5 m with acrylic glass panes at the front side, rear and top with sheet metal covering. A complete covering of the accumulator is optionally available
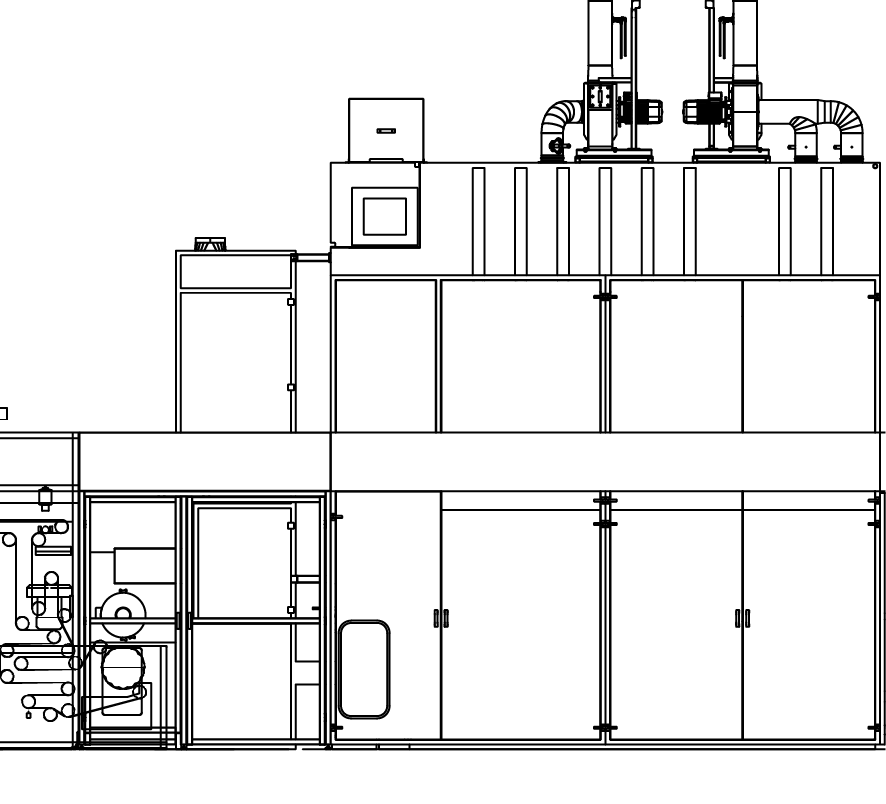
Internal coat dryer
for polymerizing the internal lacquer coat, electrically heated or alternatively by gas.
Special features
- 1,2 or 3 row transport chain with baskets
- Reduced wear-out of the transport chain and the chain wheels by cardan-based drive system
- Chain tension with weight, electronically monitored
- Easy accessibility to the dryer interior due to large doors
- Quadruple door look
- Isolated doors with special door hinges for synchronized door closing
- Large outer doors with smooth surface on the oven’s front and rear sides
- Quick and easy removal and reassembly of the shafts and chain wheels in case of service
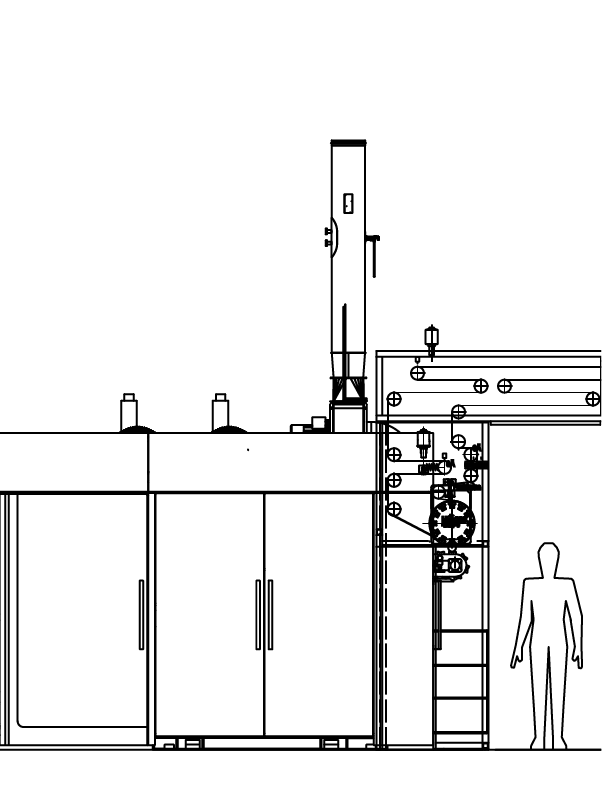
Internal coating machine
A functional lacquer is applied to seal the inside of the cylinder using moveable spray lances. In the following oven with its cooling zone the inside lacquer is cured and hardened.
Special features
- Low vibration due to solid mechanical design
- Individual vacuum circuit for machine infeed and outfeed
- Increased user comfort by direct electro-pneumatic control of the spray guns by HMI
- Shorter cleaning times by optimized exhaust performance
- Height adjustable and horizontally moveable control panel
- Combinations with different internal coating dryer options (1,2 or 3 rows)
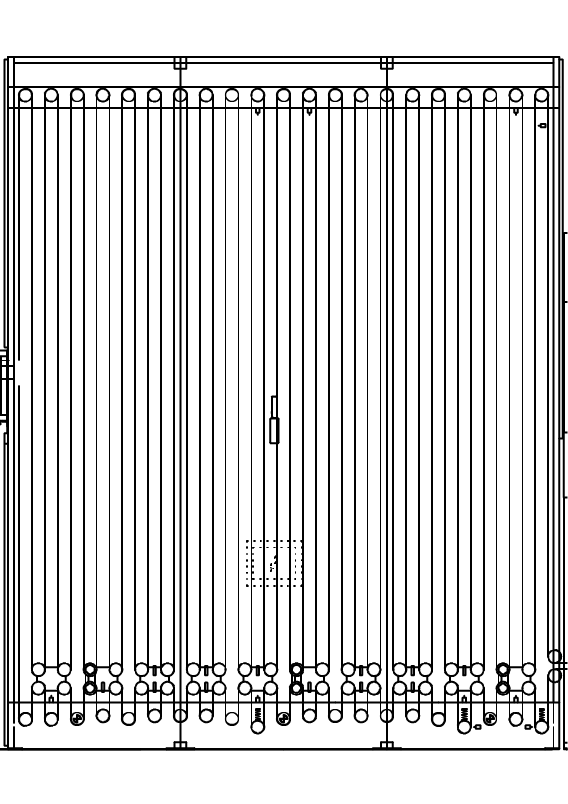
Accumulator 1
for accumulating the cylinders and compensating the asynchronous operation of the washing machine and internal coating machine.
Special features
- Three-part welded frame, mounted onto the floor with a capacity of 2100 cans
- Constant chain tension system
- Connecting traverse at accumulator outfeed to bridge a walkway
- Safety covering of the accumulator up to a height of 2,5 m with acrylic glass panes at the front side, rear and top with sheet metal covering. A complete covering of the accumulator is optionally available
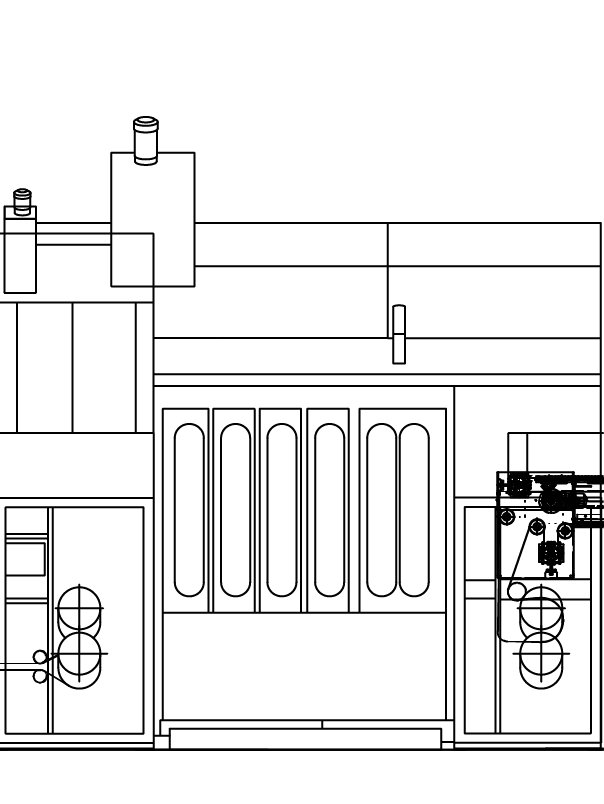
Washing machine
After pressing and trimming it is necessary to wash the lubricants from the cylinders. With our space-saving washing machines, designed in stainless steel, we offer an economic and energy-saving technology for a perfect washing result. A lot of special features allow as much customization as possible.
Technical data
Type | CWM 80-5+ |
---|---|
Diameter range (mm) | 45-80 |
Chain pitch | 6 x ¾” |
Number of washing / rinsing cabins | 5 |
Special features
- Compact, space-saving stainless steel design, washing and rinsing cabins equipped with windows
- Reliable, adaptable infeed and outfeed system ensuring easy connection to the upstream and downstream machines
- Safe and reliable infeed and outfeed transfer through vacuum drums
- Gas or electrically heated stainless-steel drying oven with long dwell time and minimum energy consumption
- Newly designed jet spray system
- Detergent dosing by means of conductivity metering and dosing pump
- Dripping area between wet and dry zone, vertically arranged pins
- Electrically heated tanks for the degreasing cabins equipped with pumps, level control and temperature control
- Automatic level control of the tanks, equipped with a safety unit against water shortage and temperature monitoring unit
- Stainless steel tanks for collecting the dripping water below the machine
- Reliable system for sucking off the oven exhaust air
- New extra platform on top of the washing cabins for a better accessibility of the dryer
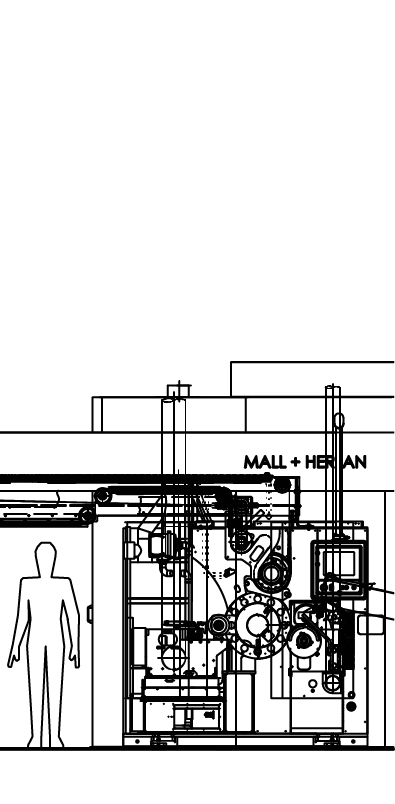
Trimming machine
The high-performance trimming machines, designed for trimming aluminium preforms to length and for brushing the body, have been fully equipped to allow flawless integration into automatic production lines. When designing the machine, particular importance was attached to ease of operation, quick tool change, easy access, solid process technology, high operational safety and little maintenance.
Technical data
Type | MHB-G |
---|---|
Can diameter (mm) | 35 - 80 |
Max. extruded overall length (mm) | 295 |
Max. trimmed can length(mm) | 280 |
Assumed wall thickness of cans (mm) | 0,2 - 1,0 |
Special features:
- Fully accessible from the front, perfect control of all movements, easy change of the brush
- Centralized lubricating system
- The trimming system produces burr less cuts and guarantees a long tool life, precision adjustment in both axial and radial direction
- Mandrel quick-change systems
- Can scrap will be shredded into small pieces for easy suckoff
- Equipment for the separation and safe discharge of the trimming scrap
- Size parts are immediately located in the correct position
- The drum-type transfer unit makes sure the cylinders are safely transferred to the downstream equipment
- Continuously operating conveyor chain at the transfer station
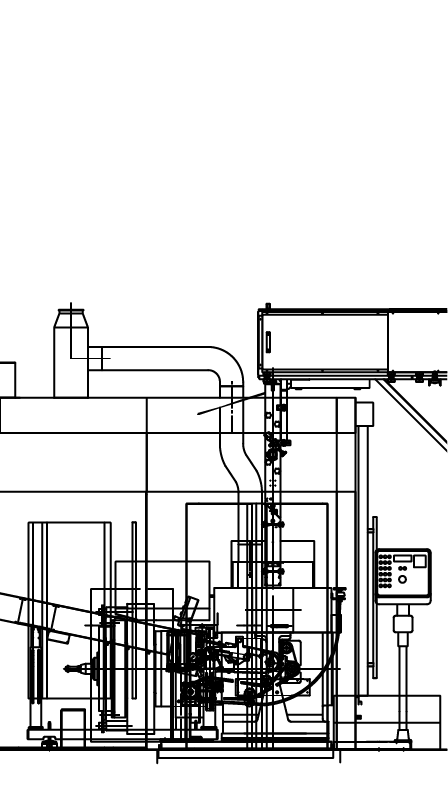
Press
If flexibility is required when producing a monoblock aluminium container, an Impact Extrusion Press is the first choice. A high performance toggle lever system produces aluminium cylinders with one stroke out of a slug. As a market leader, our presses are used all over the world for the production of monoblock aerosol cans.
Technical data
Type | Express 6000 |
---|---|
Can diameter (mm) | 53-80 |
Max. extruded can length (mm) | 310 |
Approx. wall thickness (mm) | 1,0 |
Nominal press force (kN) | 6.000 |
Special features
- Sturdy frame, separate from the drive housing, for absorbing the extrusion loads; both parts made of spheroidal graphite iron
- Compact drive of the crankshaft via pneumatically controlled clutch-brake unit with spring loaded disc brake to allow controlled or immediate stops
- Speed-variable drive, creeping speed and facility for switching to reverse motion to facilitate the setting of the tooling
- Electromotive punch adjustment for correcting the bottom thickness during production
- Swing-off type slug feed and stripper frame of the take-off unit, resulting in short set-up times and simple size-part changes, optimized for high speed production
- Automatic permanent circulatory lubrication system with filter and offline filter system
- Take-off unit operating in absolute synchronism with the outfeed conveyor, ensuring trouble-free transfer of the products even in case of short extrusions and maximum stroke rates
- Inclined slug conveyor for direct feed of flat and domed slugs to the die
- Continuous rotary slug infeed system
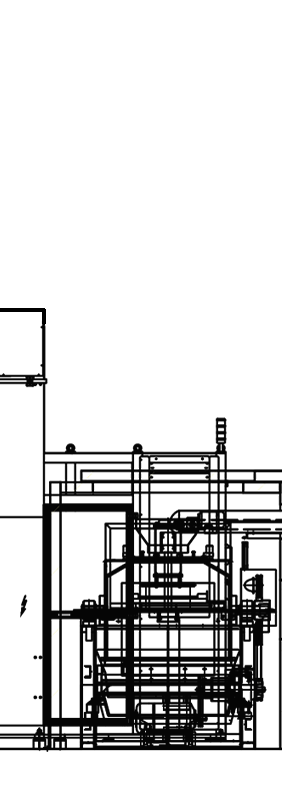
Slug infeed
In the sorting and feeding unit the slugs are separated, aligned and fed into the extrusion press.
The processing of flat or domed slugs is possible.
Special features
- Storage container with inner lining to avoid damaged slugs
- Level control of the container by means of ultrasonic sensor
- Plate type conveyor belt
- Possibility to regulate the speed of the conveyor belt for different slug sizes
- Feed chute to the clamping-type elevator
- Clamping-type slug elevator, with overload protection at the transfer of the feed chute
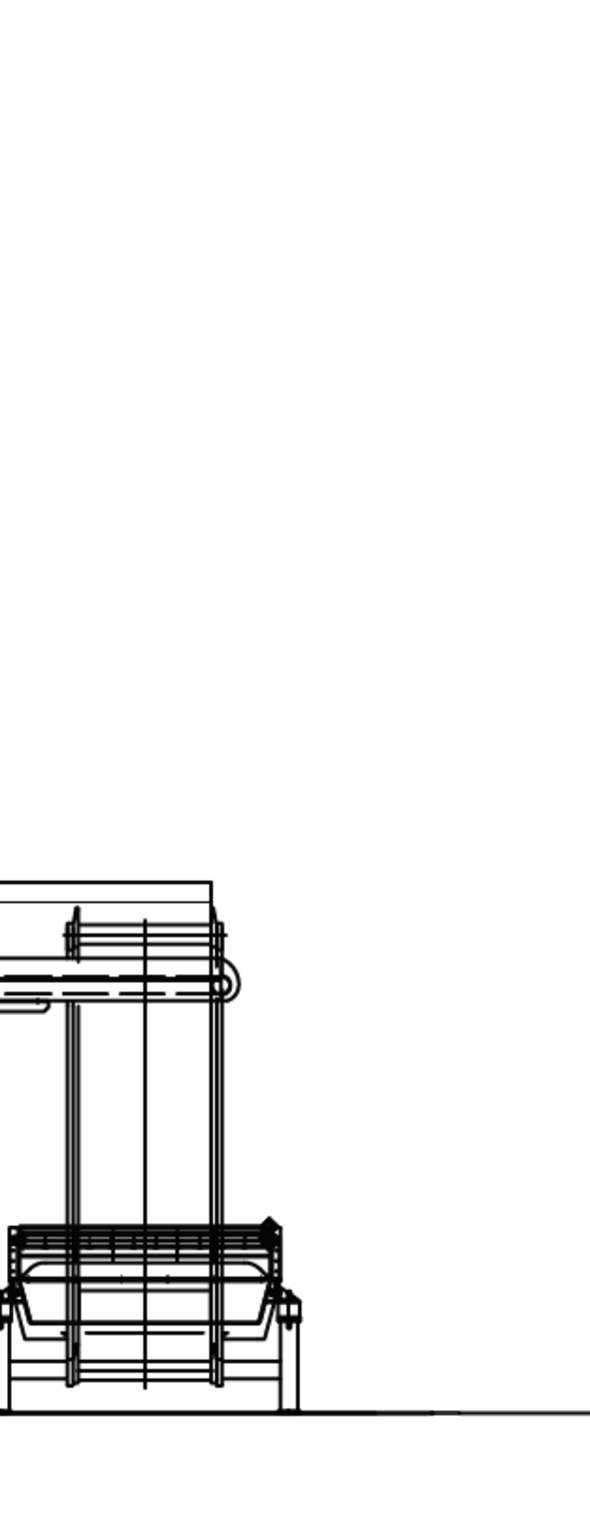
Slug lubrication
The aluminium slugs are lubricated and transported to the sorting and feeding unit.
Special features
- Storage bin for storing slugs for one lubricating process
- Feeding of slugs to the lubricating barrel by means of conveyor belt
- Abrasion-proof lining of the barrel body with cover
- Manually assisted cover lifting device, monitored by limit switches
- Elevator-type conveyor belt for transporting the slugs
DWI Production Lines:
In the DWI production line a cup is punched out of an aluminium sheet, fed by a coil. In the bodymaker the cup is ironed to a cylinder and the bottom is formed. Subsequently the cylinder is cut to length, decorated, necked and shaped to an Aluminium Bottle.
DWI
If you deal with large lot sizes and would like to save material, you should go for a DWI line. The mall//herlan DWI line is the perfect solution for a flexible and cost-effective production of aluminium cylinders out of coiled material.
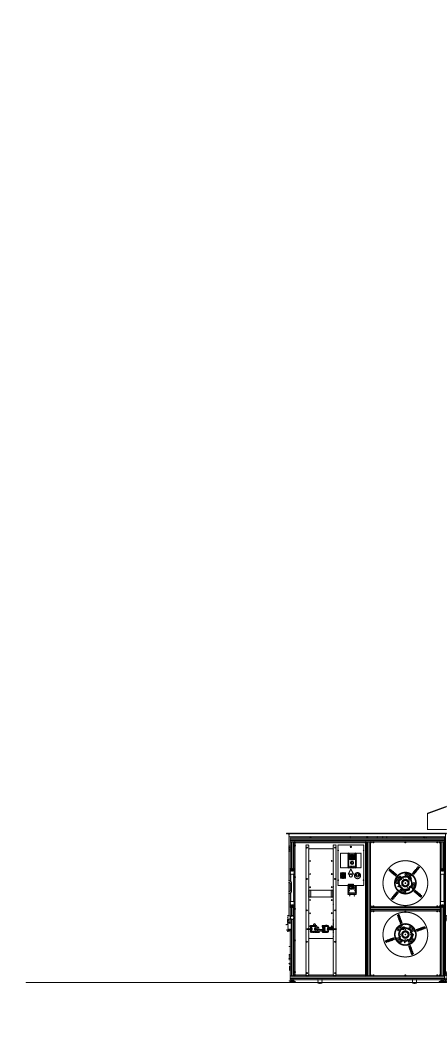
Packing machine
Different shapes and sizes of unfilled bottles cans can be palletized on this machine
Special features
- Ideal for aluminium bottles
- Optimal grouping of bottles
- Simple and quick changeover of form sets
- Synchronous can transfer
- High production reliability and security
- Aluminium bottles palletized in bundles or full-layer

Postwasher
Our customized postwashing machines are equipped with a patented spraying system to ensure low water consumption when washing off lubricants after necking.
A bypass function for the transport without washing/rinsing is included as standard.
Technical data
Type | PWM 66 |
---|---|
Max. Diameter (mm) | 66 |
Chain pitch | 5 x ¾” |
Number of washing / rinsing cabins | 2 |
Special features
- Stainless steel design, cabins equipped with windows
- Washing of the bottles in the first washing/rinsing cabin
- Rinsing of the bottles in the following rinsing cabins
- All cabins equipped with a patented spraying system with low water consumption
- Electrically heated tank for the first washing/rinsing cabin equipped with pumps, level control and temperature regulation
- Dripping area after washing, vertically arranged pins and drying blades
- Automatic level control of the tanks, equipped with safety unit against water shortage, temperature monitoring unit
- Stainless steel tank for collecting the dripping water below the washing machine
- Drying of the bottles in the gas heated oven, low-energy design
- Chain guides made of PTFE (Teflon)
- Additional blowing nozzles for drying the interior and the rim of the bottles
- Reliable system for sucking off the oven exhaust air
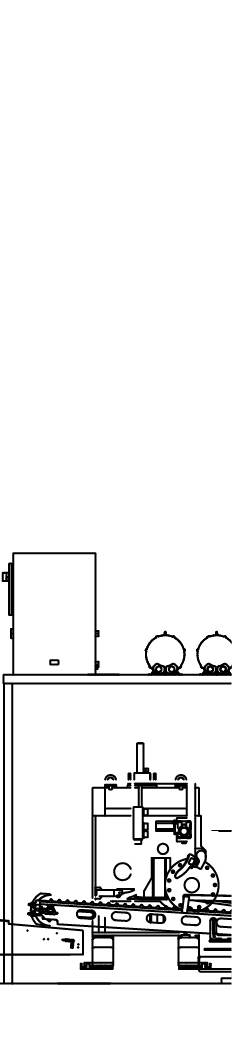
LD
Leak detector
A photocell is used to detect if rays of light fall into the bottle through micro-holes. Defective bottles are automatically ejected at the outfeed conveyor after the Leak detector. A 100% quality-control ensures that only complete secure bottles leave the line.
The Leak detector can be placed on the outfeed conveyor of the Necking machine. Alternatively it can be integrated as a stand-alone machine in the line.
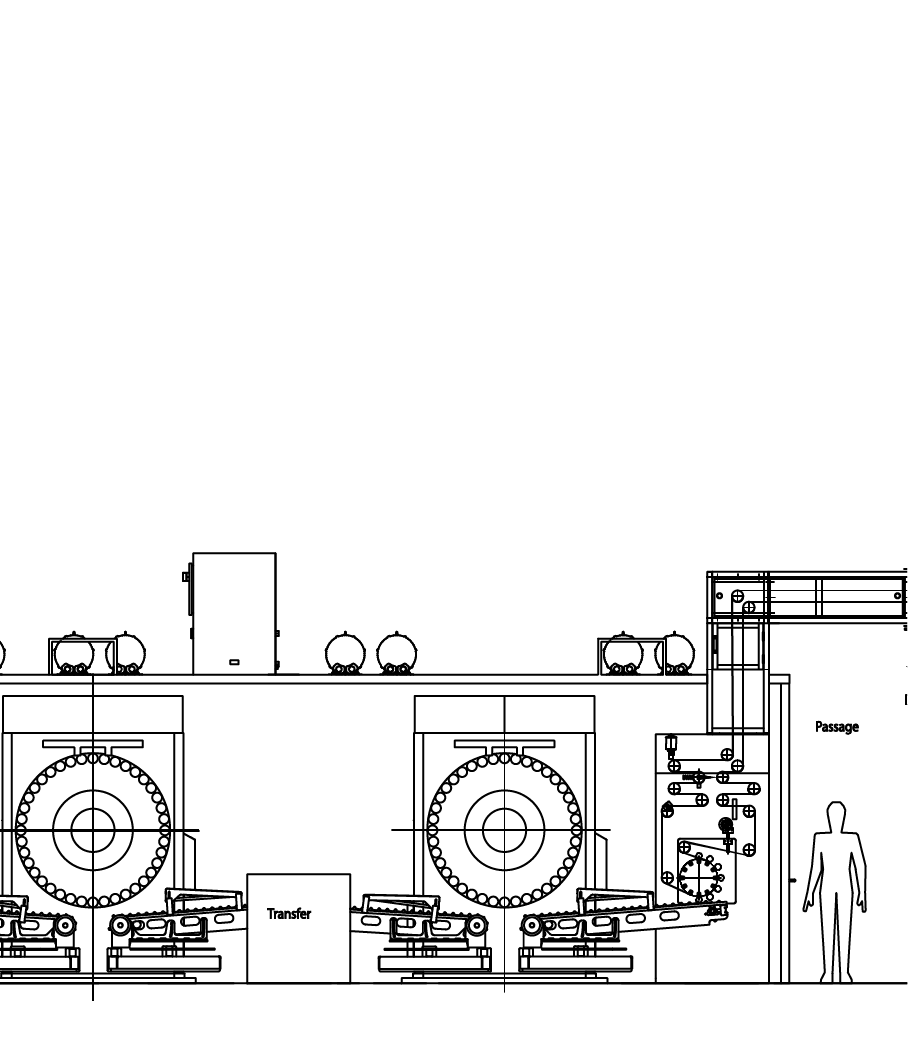
Necking machine
The cylinder is necked and shaped by necking dies up to the final bottle design. Processes as threading, curling, beading, registered em- and debossing to create unique shapes and designs fitting the needs of your customers.
Technical data
Type | C200.80VE |
---|---|
Can Diameter (mm) | 35 - 66 |
Finished product length (mm after necking) | 105 - 250 |
Number of stations | 80 |
Total stroke (mm) | 110 - 270 |
Usable stroke (mm) | 80 - 187 |
Special features
- 2 tool carrier plates including bottle transfer
- Pneumatic holding grippers with electronic control for bottle detection guarantee a constant stable position of the bottle
- Tool quick-change system for maximum product flexibility
- Compressed air-assisted necking to enable even complicated shapes
- Bottom forming unit included in the standard supply
- Maximum accessibility to the machine working area for easy handling and setting of the tools
- Optimized bottle transfer systems between conveyors and drums
- Infinitely adjustable stroke
- Electronic presetting device to set lubrication cycle frequency
- Possible application of all our proprietary tools allowing wide machining possibilities
- Frequency-controlled motors for rotating tools
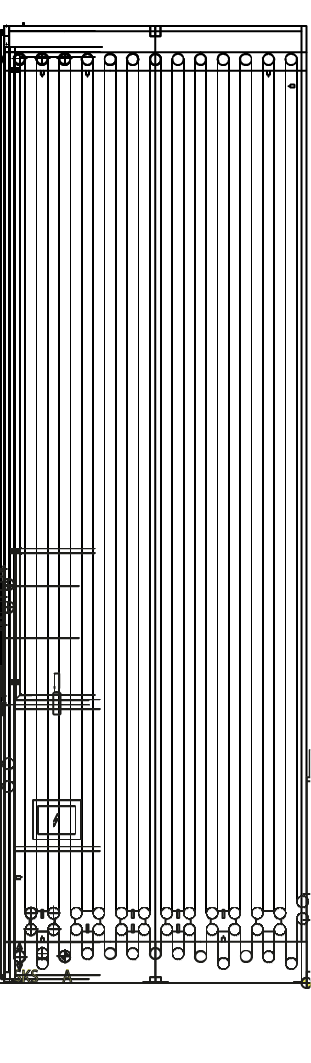
Accu 3
for accumulating the cylinders and compensating the asynchronous operation of decoration unit and necking machine.
Special features
- Two-part welded frame, mounted onto the floor
- Constant chain tension system
- Safety covering of the accumulator up to a height of 2,5 m with acrylic glass panes at the front side, rear and top with sheet metal covering. A complete covering of the accumulator is optionally available.
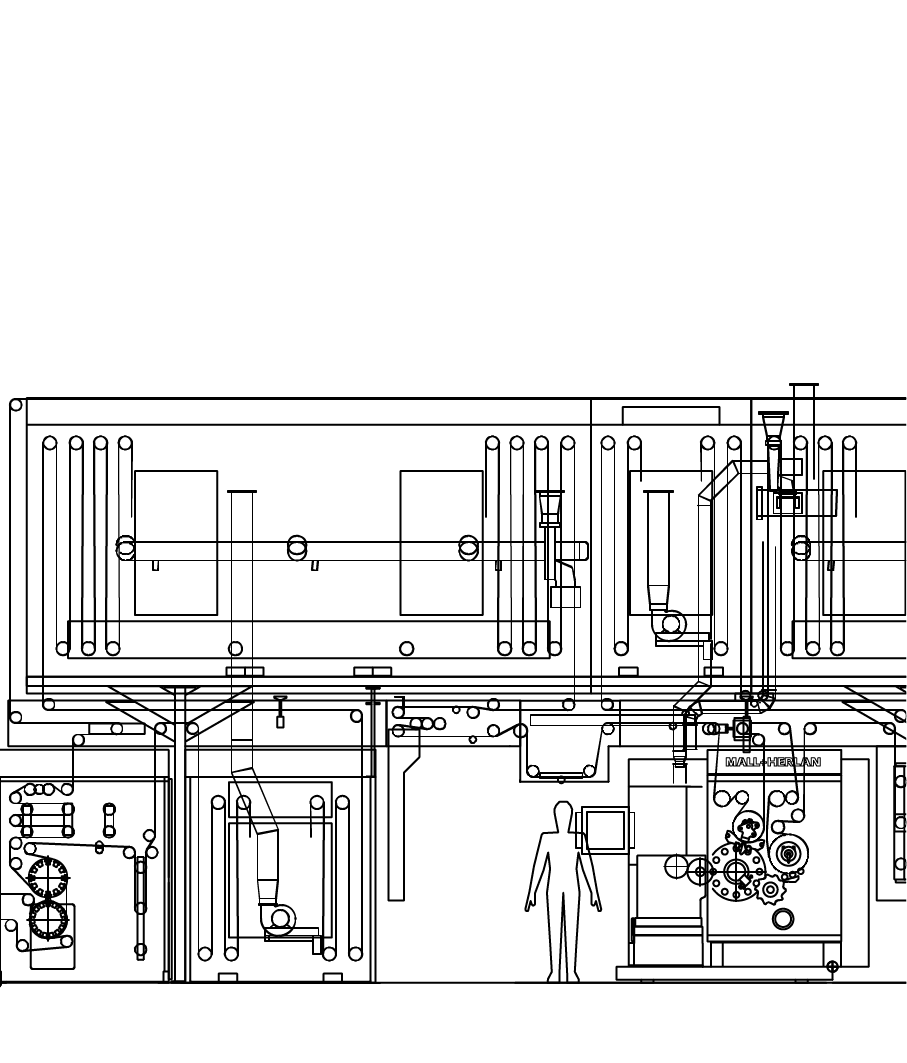
Overvarnish lacquering machine
The overvarnish is applied to protect the decoration. According to the request of your customers also special effects like matt, semi matt, gloss or haptic can be provided.
Special features
- Cylinder transfer from the conveyor chain to a mechanical take-off drum with size-independent vacuum pockets
- Mechanical indexing gear unit with 12 stations
- Mandrel quick change unit and monitoring of the correct clamping
- Infinitely variable mandrel drive by means of controlled servomotor
- Vacuum-assisted loading and steadying of the cylinders on the mandrels, before and during processing
- Three roller base-coating unit designed as V-type-coating unit
- Transfer unit with take-off control and two suction units for transporting the cylinders from the mandrels onto the chain pins
- Oven chamber with integrated chain guide
- Sprocket bearings with re-lubricating facility, installed outside the oven in an aluminium casing sealed towards the rear wall of the oven
- Possibility of cylinder sampling for test purposes from the pins of the dryer chain, after drying of the clear varnish.
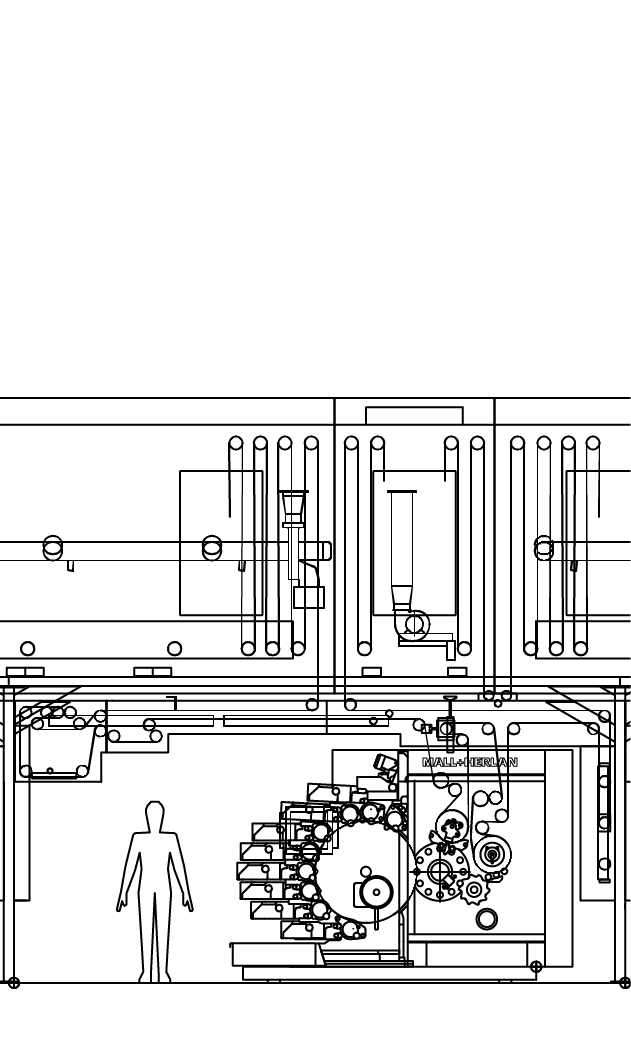
Printing machine
The printing unit, which can apply up to 9 colours, ensures the widest possible decoration variety for aluminium bottles
Special features
- Cylinder transfer from the conveyor chain to a mechanical take-off drum with size-independent vacuum pockets
- Mechanical indexing gear unit with 12 stations
- Mandrel quick change unit and monitoring of the correct clamping
- Infinitely variable mandrel drive by means of controlled servomotor
- Vacuum-assisted loading and steadying of the cylinders on the mandrels, before and during processing
- Printing unit with up to 9 colours
- Transfer unit with take-off control and two suction units for transporting the cylinders from the mandrels onto the chain pins
- Oven chamber with integrated chain guide
- Sprocket bearings with re-lubricating facility, installed outside the oven in an aluminium casing sealed towards the rear wall of the oven
- Possibility of cylinder sampling for test purposes from the pins of the dryer chain, after drying of the printing inks.
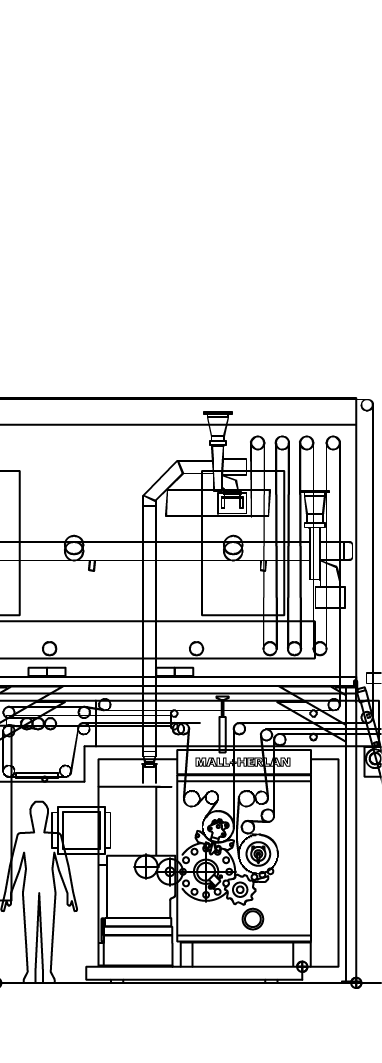
Basecoat
Basecoat lacquering machine
The cylinder receives the base coat which is important for the stain resistance and excellent print quality. The base coat is dried in the first oven chamber of the decoration drying oven.
Special features
- Cylinder transfer from the conveyor chain to a mechanical take-off drum with size-independent vacuum pockets
- Mechanical indexing gear unit with 12 stations
- Mandrel quick change unit and monitoring of the correct clamping
- Infinitely variable mandrel drive by means of controlled servomotor
- Vacuum-assisted loading and steadying of the cylinders on the mandrels, before and during processing
- Three roller base-coating unit designed as V-type-coating unit
- Transfer unit with take-off control and two suction units for transporting the cylinders from the mandrels onto the chain pins
- Oven chamber with integrated chain guide
- Sprocket bearings with re-lubricating facility, installed outside the oven in an aluminium casing sealed towards the rear wall of the oven
- Possibility of cylinder sampling for test purposes from the pins of the dryer chain, after drying of the basecoat
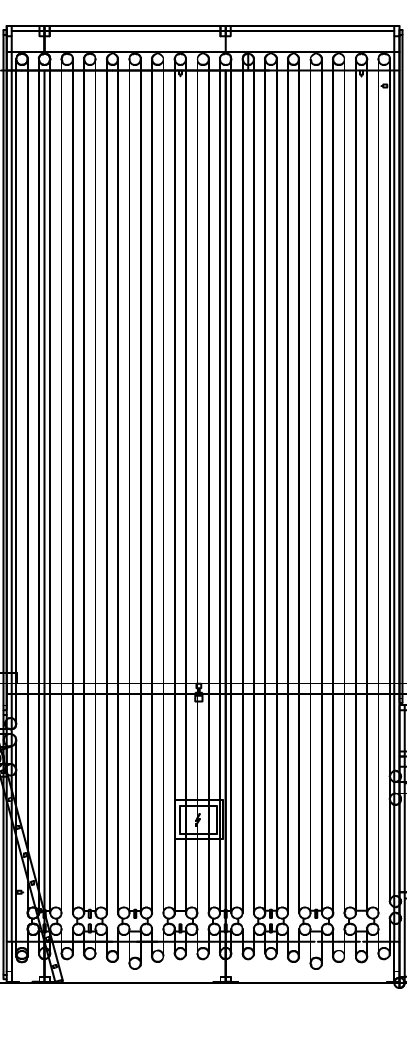
Accumulator 2
for accumulating the cylinders and compensating the asynchronous operation of internal coating machine and decoration unit.
Special features
- Four-part welded frame, mounted onto the floor
- Constant chain tension system
- Safety covering of the accumulator up to a height of 2,5 m with acrylic glass panes at the front side, rear and top with sheet metal covering. A complete covering of the accumulator is optionally available.
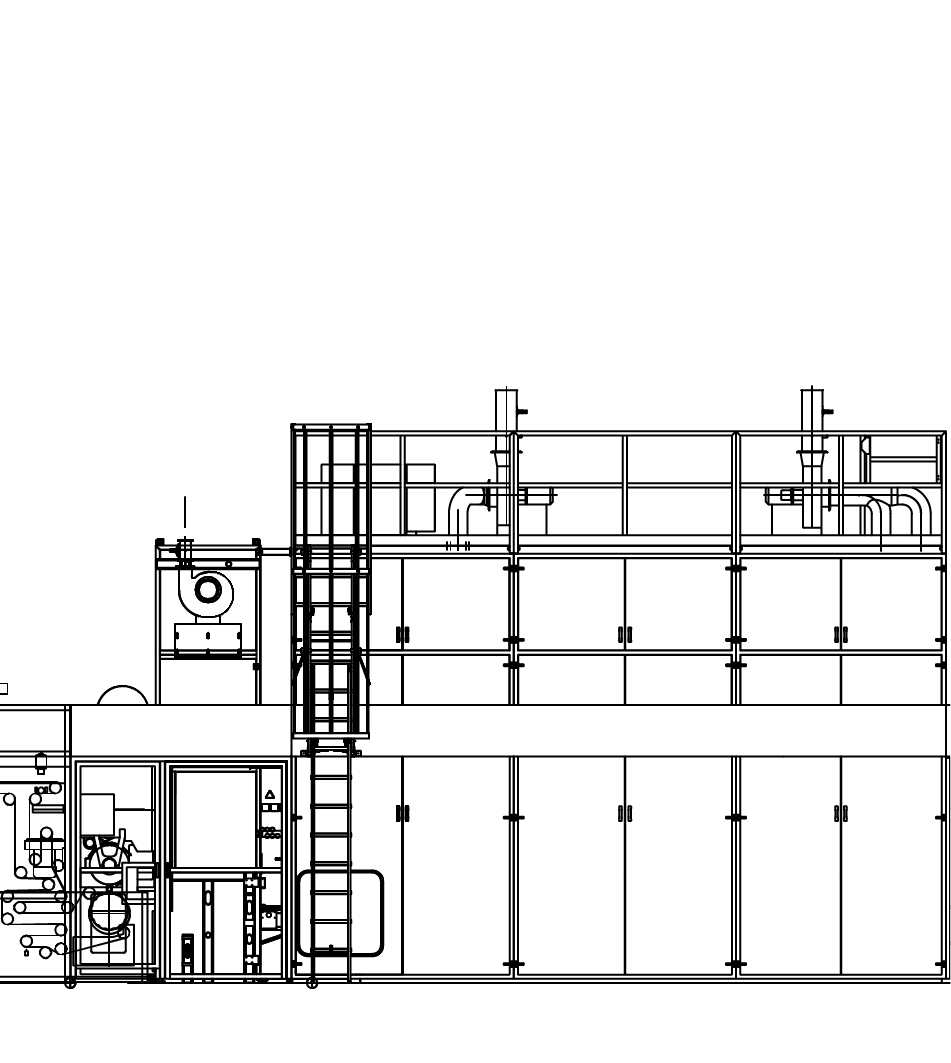
Internal coat dryer
for polymerizing the internal lacquer coat, electrically heated or alternatively by gas.
Special features
- 1,2 or 3 row transport chain with baskets
- Reduced wear-out of the transport chain and the chain wheels by cardan-based driven system
- Chain tension with weight, electronically monitored
- Easy accessibility to the dryer interior due to large doors
- Quadruple door look
- Isolated doors with special door hinges for synchronized door closing
- Large outer doors with smooth surface on the oven’s front and rear sides
- Quick and easy removal and reassembly of the shafts and chain wheels in case of service
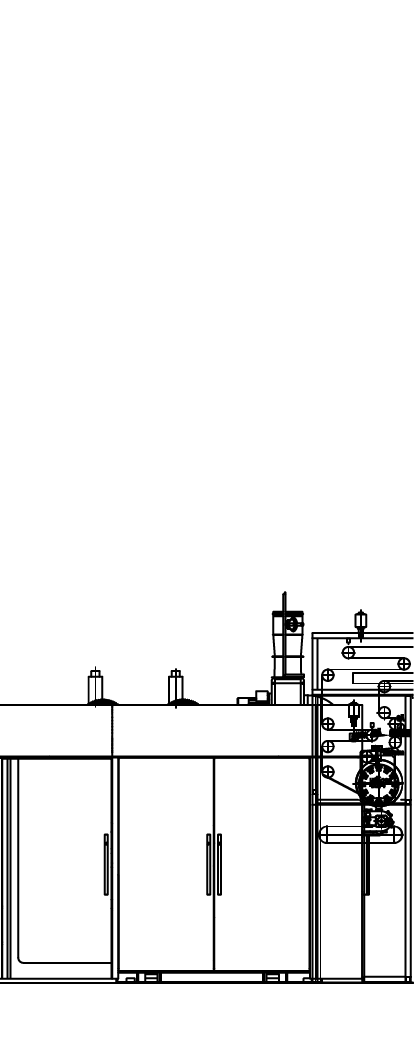
Internal coating
Internal coating machine
A functional lacquer is applied to seal the inside of the cylinder using moveable spray lances. In the following oven with its cooling zone the inside lacquer is cured and hardened.
Special features
- Low vibration due to solid mechanical design
- Individual vacuum circuit for machine infeed and outfeed
- Increased user comfort by direct electro-pneumatic control of the spray guns by HMI
- Shorter cleaning times by optimized exhaust performance
- Height adjustable and horizontally moveable control panel
- Combinations with different internal coating drier options (1,2 or 3 rows)
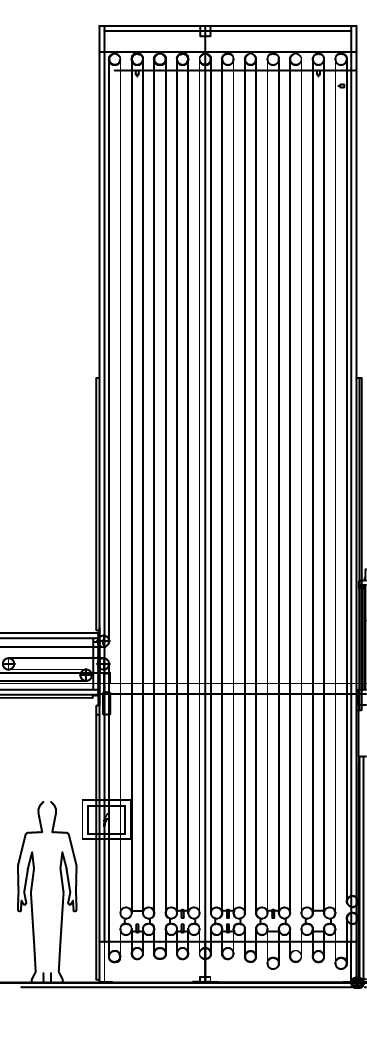
Accumulator 1
for accumulating the cylinders and compensating the asynchronous operation of the washing machine and internal coating machine.
Special features
- Three-part welded frame, mounted onto the floor
- Constant chain tension system
- Connecting traverse at accumulator outfeed to bridge a walkway
- Safety covering of the accumulator up to a height of 2,5 m with acrylic glass panes at the front side, rear and top with sheet metal covering. A complete covering of the accumulator is optionally available.
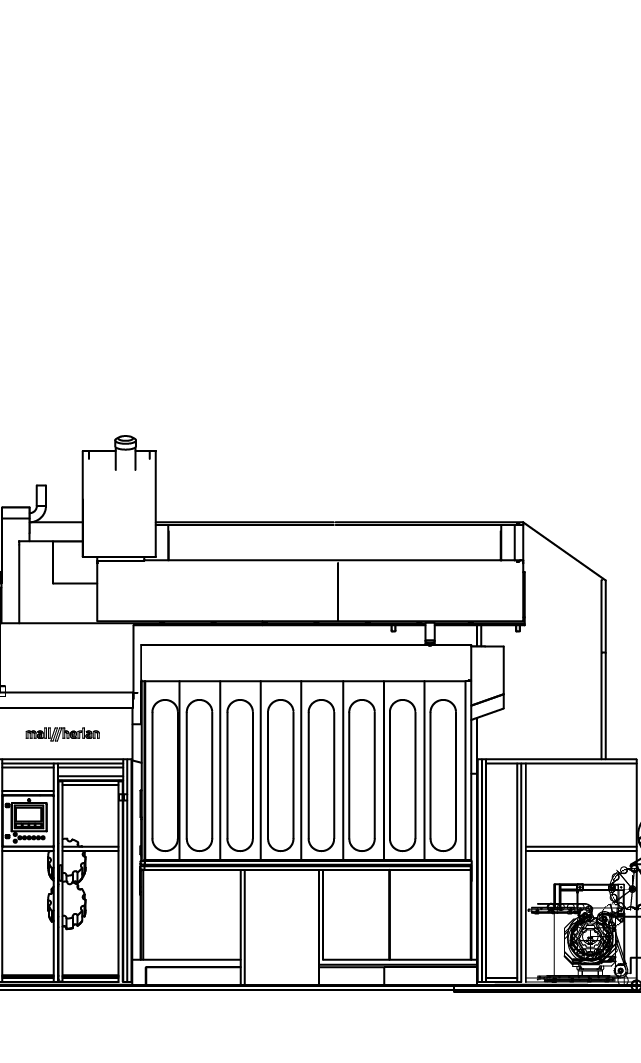
Washing machine
After ironing and trimming it is necessary to wash the lubricants from the cylinders. With our space-saving washing machines, designed in stainless steel, we offer an economic and energy-saving technology for a perfect washing result.
A lot of special features allow as much customization as possible.
Technical data
Type | CWMx 66-8 |
---|---|
Diameter range (mm) | 45-66 |
Chain pitch | 5 x ¾” |
Number of washing / rinsing cabins | 8 |
Special features
- Compact, space-saving stainless steel design, washing and rinsing cabins equipped with windows
- Reliable, adaptable infeed and outfeed system ensuring easy connection to the upstream and downstream machines
- Safe and reliable infeed and outfeed transfer through vacuum drums
- Gas or electrically heated stainless-steel drying oven with long dwell time and minimum energy consumption
- Newly designed jet spray system
- Detergent dosing by means of conductivity metering and dosing pump
- Dripping area between wet and dry zone, vertically arranged pins
- Electrically heated tanks for the degreasing cabins equipped with pumps, level control and temperature control
- Automatic level control of the tanks, equipped with a safety unit against water shortage and temperature monitoring unit
- Stainless steel tanks for collecting the dripping water below the machine
- Reliable system for sucking off the oven exhaust air
- New extra platform on top of the washing cabins for a better accessibility of the dryer
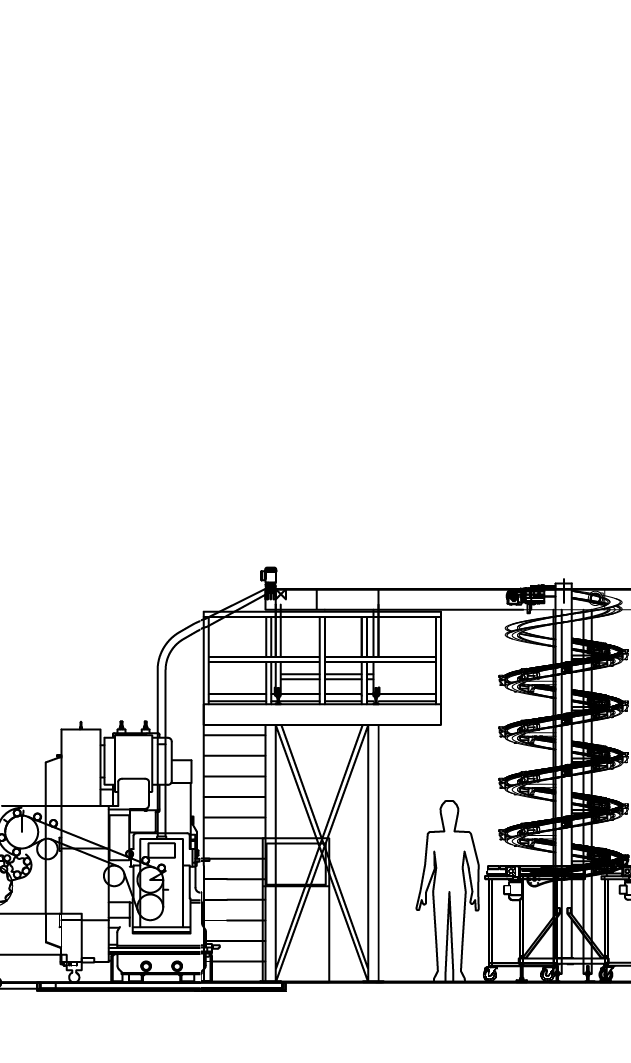
Bodymaker
Bodymaker
with integrated trimming system
In a first step the cup is redrawn to its final circumferences. The cylinder is then directly drawn through up to four rings to reduce the wall thickness up to 65% and consequently extend the length (Ironing process). With the trimming system the cylinder is cut to the correct length.
Special features
- Foundation plate
- Coolant system
- Trimming system
- Transfer to succeeding mall//herlan washing machine
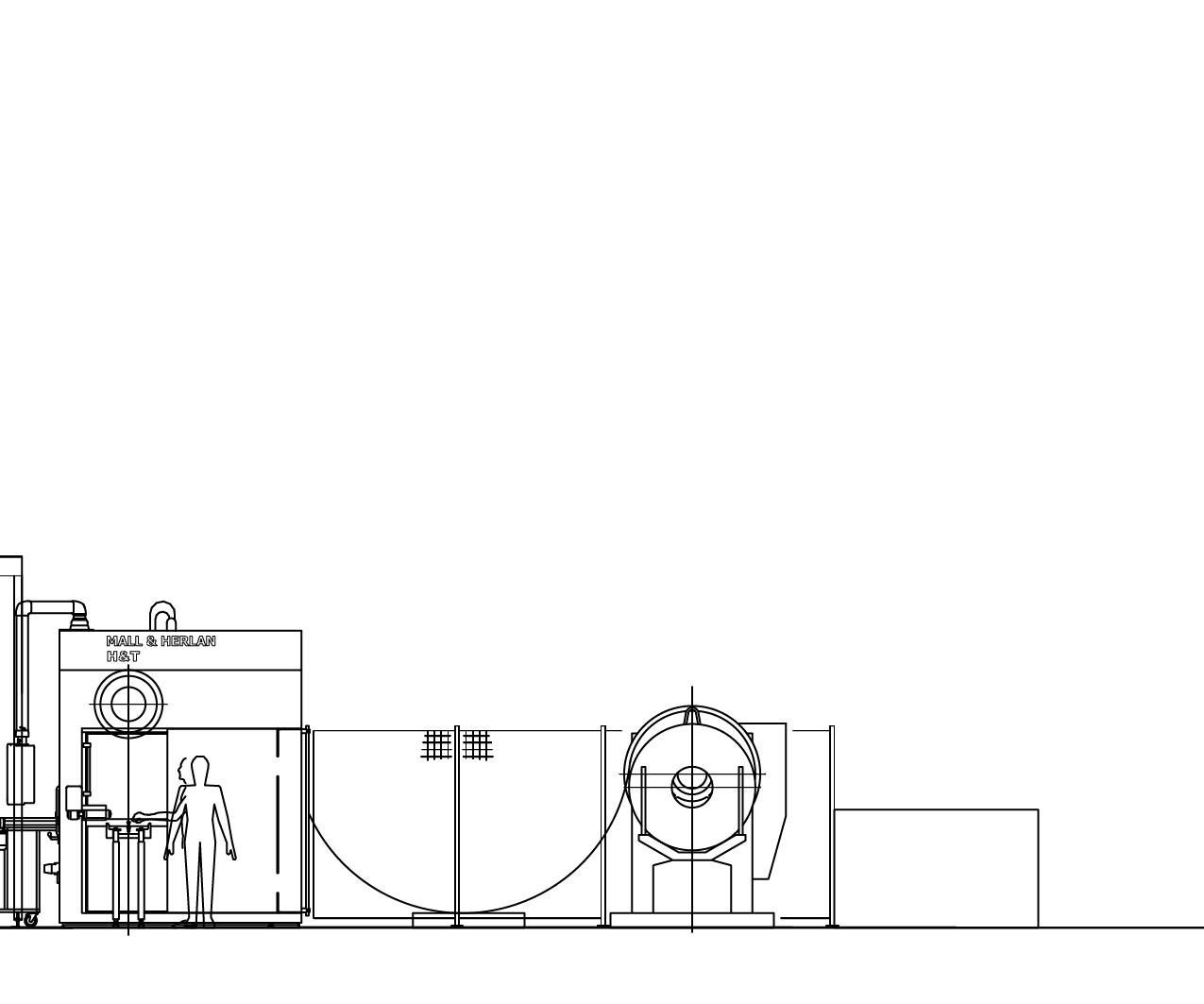
Cupper
incl. uncoiler and transfer system
The aluminium coil is moved from the upender onto the uncoiler. The uncoiled metal is pulled longitudinally into the cupper. The operator can configure the punching process with maximum flexibility to suit the specific requirements by defining the number of active tools and the number and width of the horizontal steps via the control system. A blank holder fixes the material and a circular knife die-cuts a disk. With a subsequent punch the disc is deep-drawn into a cup. A conveyor system transfers cups to the bodymaker.
Special features
- Optimized tooling accessibility due to removing the tool by a tool carrier
- Quick change of die set
- Flexible number of max. 5 dies possible
- Optimum utilisation of over 87% of the material
- No decoupled foundation needed because of vibration absorption between frame and foundation
Markets
Aluminium bottles, a trendsetting packing for a modern lifestyle, produced on our customised production lines for aluminium bottles. A large variety of bottle designs, serveral closure options like Thread, Crown or Maxi-P and the possibility of full body shaping allow as much individualisation as needed.
The mall//herlan lines combine full process knowledge and a great production range to make our customers the most successful players in their markets, as
- Carbonated soft drinks
- Beer and Spirits
- Functional- and energy drings
- Tea and coffee
- Juices
- Chemical industry
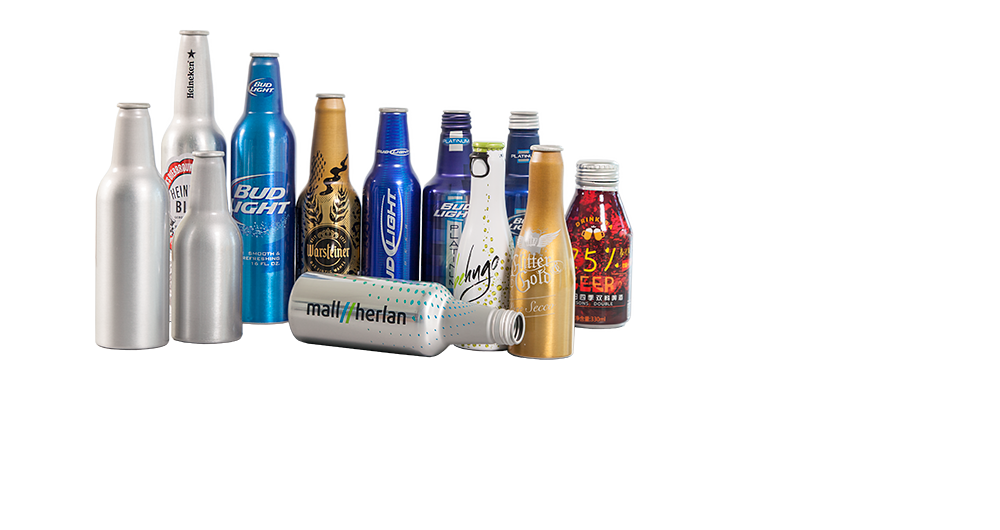